プラスチック部品のマシニング加工に関するガイド
プラスチックのマシニング加工にはどのような方法があり、高機能の熱可塑性部品をマシニング加工する場合には、どのような条件を考慮すべきなのでしょうか。このガイドでは、特に一般的なプラスチックマシニング加工法を取り上げ、三菱ケミカルグループ製のさまざまなエンジニアリングポリマープラスチックを扱う際に役立つヒントとデータを提供します。
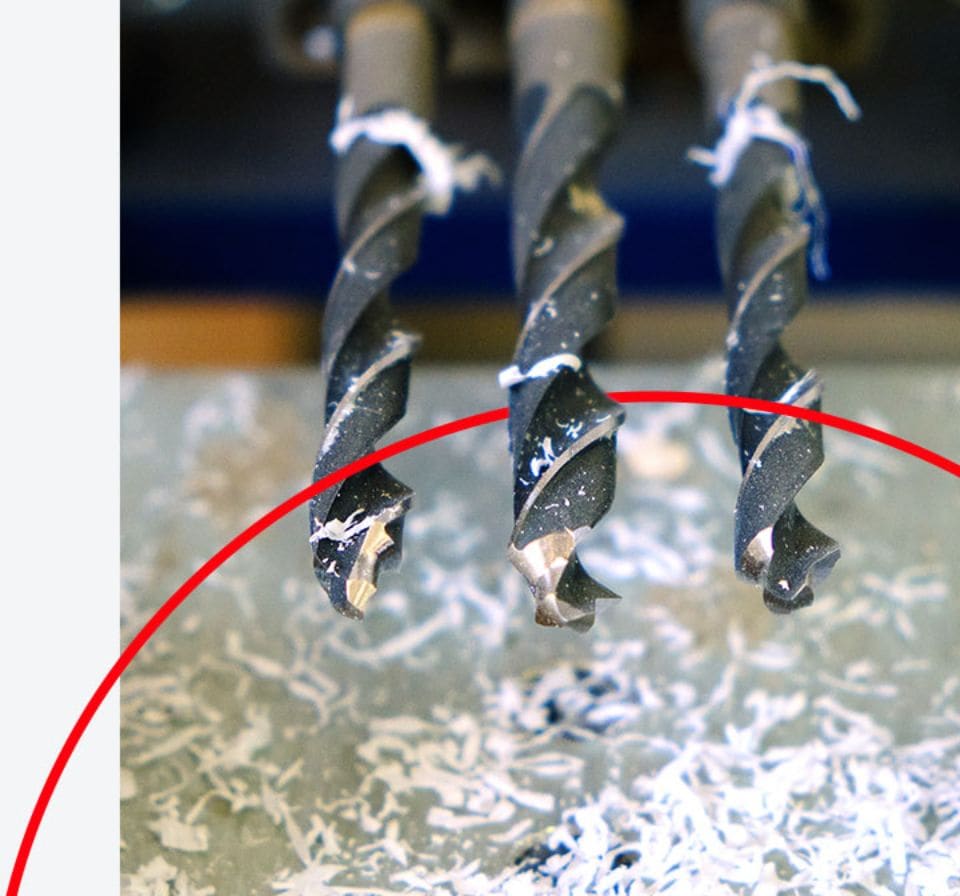
プラスチックは機械的特性、化学的特性、および軽量性に優れているので、幅広い工学応用で徐々に金属に取って代わろうとしています。金属部品を製造するために使用されているマシニング加工法の多くは、プラスチックにも使用されます。ただし、プラスチックのマシニング加工に関するベストプラクティスは、金属をマシニング加工する場合とはかなり異なります。
プラスチックは、マシニング加工手順に影響を与える次のようなさまざまな特性を示します。
- プラスチックの熱膨張は金属の熱膨張の10倍まで進行します。
- プラスチックは、金属よりゆっくり放熱するため、局所的な過熱の危険性が高まります。
- プラスチックは金属よりかなり低い温度で軟化と融解が起こります。
- プラスチックは金属よりはるかに弾力性があります。
材料選定から適切な工具まで、送り量から安定化法まで、部品製造業者は、プラスチックをマシニング加工する際に良好な結果を得るためにさまざまな要因を考慮する必要があります。以降のガイドラインでは、特に一般的なプラスチックマシニング加工法を取り上げ、三菱ケミカルグループ製のエンジニアリングポリマーを操作するうえで役立つヒントやデータを提供します。
以下の概要を読むか、「工作機械オペレーター用ツールキット」をダウンロードしてください。この電子書籍は、さまざまな三菱ケミカルグループ製の材料に推奨される速度と工具も取り上げている、製造に関する包括的なガイドです。
一般的なプラスチックのマシニング加工プロセス
-
このセクションでは、プラスチックエンジニアリング部品をマシニング加工する最も一般的な方法を取り上げ、それぞれで最良の結果を達成するためのガイドラインとヒントを提供します。
適切なマシニング加工は、部品の寸法と性能を実現するために不可欠です。不適切なマシニング加工は、完成部品内に応力を生じさせ、その機械的特性に悪影響を及ぼし、早期部品故障の危険性を高める可能性があります。
マシニング加工中の応力の主な原因は次のとおりです。
• 切れない工具または設計が不適切な工具の使用
• 不適切な速度や送り量から発生した過剰な熱
• 大量の材料を取り除くマシニング加工(通常は、材料成形の片側から) -
ねじ切りとは何かねじ立てとは何か
ねじ立てとねじ切りは、ねじ山を作るために使用される2つのマシニング加工法です。ねじ切りはダイ工具を使用して雄ねじを切るプロセスであるのに対して、ねじ立てはタップ工具を使用してドリル穴の内側にねじを形成するプロセスです。
プラスチックと金属へのねじ切りとねじ立て
プラスチックをねじ切りまたはねじ立てする場合の主な考慮事項は、プラスチックは金属より切欠き脆性が高いということです。一部のポリマー材料は、特に、ファインピッチ手順においてねじ切り中に裂ける可能性があります。
プラスチックのねじ切りに関するヒント
プラスチックのねじ切りは、1点で超硬インサートを使用して行う必要があります。終点では0.001"の経路を4~5回たどります。冷却剤の使用を推奨します。
プラスチックのねじ立てに関するヒント
プラスチックをねじ立てする場合は、特定の2枚刃タップ付きのドリルを使用します。先端形成中はタップを清潔に保ちます。ねじ立て中の冷却剤使用も推奨します。
-
フライス削りとは何か
フライス削りは、固定されたプラスチック形状に高速の円筒状切削工具を当てて、軸上でカッターを移動させながらさまざまな方向に形状を削り取るマシニング加工法です。コンピュータによる数値制御(CNC)フライス削りは、プラスチックフライス削りの精度と効率性を高めます。
プラスチックと金属のフライス削り
プラスチックをフライス削りする場合は、作業台上の部品を適切に固定し、高速切削工具からの振動を最小限に抑えることが不可欠です。そうしなかった場合は、形状移動が原因のチャッターマークや精度の低下につながる可能性があります。
プラスチックのフライス削りに関するヒント
- 下向き削りとも呼ばれる下向きフライス削りは、上向きフライス削りより推奨されています。
- ミルベッド上の固定を十分に行うと、高速のテーブル移動や速い主軸速度が可能になります。
- 形状はきつく固定しすぎないようにする必要があります。変形したり、裂けたりする可能性があります。
- 正面フライス削りの場合は、正形状カッターボディを使用します。
-
のこ引きとは何か
のこ引きは、バンドソー、テーブルソー、またはその他の特化した機器を使用して材料を複数の断片に切削することを伴うマシニング加工法です。
プラスチックと金属ののこ引き
プラスチックと金属ののこ引きの主な違いは、軟化温度や融解温度が低いことが原因で、のこ刃から発生する熱がプラスチック部品に悪影響を及ぼす可能性があることです。プラスチックをのこ引きする際は、刃の速度、材料の温度特性、および形状の厚みを考慮することが不可欠です。
のこぎりの選定に関するヒント
- バンドソーは、用途が広く、直線カット、連続曲線カット、および不規則なカットに適しています。
- テーブルソーは、直線カットに適しており、複数の厚みや分厚い横断面(適切な馬力で最大4")のカットに使用できます。
のこ刃の選定に関するヒント
- 刃レーキが0°で刃セットが3~10°のリップと組み合わせ刃が、一般的なのこ引きで摩擦熱を削減するのに最適です。
- セットなしのホローグラインドされた丸のこ刃は、最大3/4"の厚みのスムーズなカットを実現します。
- 炭化タングステン刃は、耐久性があり、最適な表面仕上げを実現します。
-
穴あけとは何か穴ぐりとは何か
穴あけは、先端がとがった螺旋状工具を使用して円筒穴や通し穴を作成するマシニング加工法です。穴ぐりは、ドリル穴を広げたり、仕上げたりするための二次プロセスです。
プラスチックと金属の穴あけと穴ぐり
穴あけ操作中、特に、穴の深さが穴の直径の2倍を超える場合は、プラスチックの断熱性を考慮する必要があります。過剰な発熱は、チッピング、粗面、および不適切な許容範囲の原因になる可能性があります。
プラスチックの穴あけに関するヒント小径穴の場合(1/32”~1”)
- 普通は、高速スチールツイストドリルで十分です。
- 削り屑の除去を改善するために、頻繁な引き抜き(ペック穴あけ)を推奨します。
- スロースパイラル(ローへリックス)ドリルを使うと、削り屑の除去を改善できます。
For large diameter holes (1” and greater)
- A slow spiral (low helix) drill or general-purpose drill bit ground to a 118° point angle with 9° to 15° lip clearance is recommended. The lip rake should be ground (dubbed off) and the web thinned.
- Avoid hand feeding - drill grabbing can result in microcracks.
- It is generally best to drill a pilot hole (maximum 1/2” diameter) using 600 to 1000 rpm and a positive feed of 0.005” to 0.015” per revolution.
- Secondary drilling at 400 to 500 rpm at 0.008” to 0.020” per revolution is required to expand the hole to larger diameters.
For especially notch-sensitive materials (such as Ertalyte® PET-P and glass reinforced materials)
- A two-step process involving both drilling and boring minimizes heat build-up and reduces the risk of cracking.
- Firstdrill a 1” diameter hole using an insert drill at 500 to 800 rpm with a feed rate of 0.005” to 0.015” per revolution.
- Next bore the hole to final dimensions using a boring bar with carbide insert with 0.015” to 0.030” radii at 500 to 1000 rpm and a feed rate of 0.005” to 0.010” per revolution.
-
旋削とは何か
旋削は、プラスチック形状が固定旋盤の周りを回転するマシニング加工プロセスです。旋削は、特に、共通の回転軸に沿って対称になっている部品のマシニング加工に有用です。
プラスチックと金属の旋削
他のプラスチックマシニング加工プロセスと同様に、旋削は熱を発生させます。プラスチック部品の破損を防ぐために、材料の温度特性とともに、回転速度、工具選定、および冷却剤のすべてを慎重に検討する必要があります。
プラスチックの旋削に関するヒント
- 旋削操作には、正形状と研磨された外周を備えたインサートが必要です。
- 研磨された外周と滑らかな上面は、一般的に、インサート上の材料堆積を減らし、表面仕上げの時間を短縮します。
- 多くの場合、プラスチック旋削操作には微粒子C-2カーバイドが推奨されています。
マシニング加工でのその他の処理
-
部品やマシニング加工プロセスの要件に応じて、仕上がりを良くするために冷却剤および/または焼きなましが推奨される場合があります。このセクションでは、プラスチック部品のマシニング加工に適用可能な冷却剤と焼きなましの使用を取り上げます。
-
冷却剤とは何か
冷却剤は局所的な摩擦熱の発生を抑えるため、マシニング加工の結果が良くなり、工具の寿命が延びます。エンジニアリングプラスチックをマシニング加工する場合によく使用される冷却剤にはいくつかのタイプがあります。これには、空気、ドライアイス、スプレーミスト、および特別に開発された冷却剤が含まれます。
冷却剤が推奨される場合ほとんどのマシニング加工作業やほとんどのエンジニアリングプラスチックに冷却剤は必要ありません。ただし、次のようなケースでは冷却剤を推奨します。
- プラスチックを穴あけまたは切断する場合 - 高い摩擦熱を発生させる2つのプロセス。
- 特に切欠き脆性材料(Ertalyte™ PET-P、Duratron™ PAI、Duratron™ PBIなど)やガラス強化製品またはカーボン強化製品をマシニング加工する場合。
- 最適な表面仕上げと精密公差を達成する必要がある場合。
冷却剤の選定に関するヒント
- スプレーミストと圧縮空気は、非常に効果的な切削界面の冷却手段です。
- 汎用石油系切削液は、さまざまな金属とプラスチックに適していますが、非晶質プラスチック(Altron™ PC、Sultron™ PSU、Sultron™ PPSU、Duratron™ U1000 PEIなど)の応力亀裂の要因となる可能性があります。
- ほとんどのプラスチックに適切な冷却液はTrim E190とTim Sol LC SFの2つです。
-
アニーリングとは何か
アニーリングは、プラスチックの物理特性を向上させ、その延性を高め、その硬度を下げることによって、形状をマシニング加工しやすくする熱処理プロセスです。アニーリングは、プラスチック内部からの圧力を和らげるのに役立つため、一定期間マシニング加工する部品の寸法安定性を高めます。アニーリングプロセスには、プラスチック形状を所定の期間に融解温度の半分まで加熱することと特定の速度で冷却することが含まれます。
マシニング加工前のアニーリング
三菱ケミカルグループのアドバンスドマテリアルズ本部が提供しているすべてのプラスチック材料成形には、製造過程で発生する可能性のある内部応力を最小限に抑える独自の応力除去サイクルを使用して焼きなましを行っています。これにより、材料がマシニング加工中と加工後に寸法的に安定した状態を維持することが保証されます。
マシニング加工後のアニーリング
寸法要件や性能要件を満たすためにマシニング加工後のアニーリングを必要とするマシニング加工プラスチック部品はほとんどありませんが、マシニング加工後のアニーリングには次のようなメリットがあります。
- 耐化学性の向上 - PC、PSU、およびPEI材料は、マシニング加工後の焼きから応力クレージングを低減する恩恵を受ける可能性があります。
- 平坦性の向上と許容範囲の厳密化 - 精度平坦性と非対称コンターが必要な超精密公差部品には、マシニング加工操作中の中間焼きなましが必要な場合があります。
- 高い圧力速度と低い摩耗PAI - 高い圧力速度または可能な限り低い摩耗係数が必要な押し出しまたは射出成形Duratron™ PAI部品は、マシニング加工後のポストキュアの恩恵を受けます。このポストキュアによって、摩耗特性が最適化されます。このようなサイクルから恩恵を受けるのはPAIだけです。
プラスチックのアニーリングに関するヒント- 平坦性の向上は、粗いマシニング加工、アニーリング、および超軽切り込みによる仕上げマシニング加工によって実現可能です。
- マシニング加工中の応力の可能性を低減するには、特定の材料に関する製造ガイドラインを確認してください。材料タイプごとにガイドラインが異なることに注意してください。
- 歪みを避けるために部品が必要な形状または平面に固定されていることを確認してください。部品が全サイクルを終了し、表面が冷たくなるまで外さないでください。
- アニーリング後は、限界寸法までの仕上げマシニング加工を実施する必要があります。
- 横断面が薄い場合は、加熱時間と保持時間を変えることができます。
エンジニアリングプラスチックのトラブルシューティングに関するガイドライン
-
- テーパー穴
- 間違ってとがらせたドリル
- 不十分なクリアランス
- 送りが重すぎる
- 焼けたまたは溶けた表面
- 不正なドリルタイプ
- 間違ってとがらせたドリル
- 送りが軽すぎる
- 切れないドリル
- ウェブが厚すぎる
- 表面の削り屑
- 送りが重すぎる
- クリアランスが大きすぎる
- レーキが大きすぎる(規定された薄いウェブ)
- チャッター
- クリアランスが大きすぎる
- 送りが軽すぎる
- ドリルの突出部が大きすぎる
- レーキが大きすぎる(規定された薄いウェブ)
- 内径上の送りマークまたは渦巻線
- 送りが重すぎる
- ドリルが中心に置かれていない
- ドリルグラウンドが中心に置かれていない
- 穴が大きすぎる
- ドリルグラウンドが中心に置かれていない
- ウェブが厚すぎる
- 不十分なクリアランス
- 送り量が重すぎる
- 先端角が大きすぎる
- 穴が小さすぎる
- 切れないドリル
- クリアランスが大きすぎる
- 先端角が小さすぎる
- 穴が同心ではない
- 送りが重すぎる
- 主軸速度が遅すぎる
- 次の断片へのドリルの入りが遠すぎる
- 切断工具がニブから離れている、偏ったドリル
- ウェブが厚すぎる
- 開始時のドリル速度が重すぎる
- ドリルが中心に取り付けられていない
- ドリルが正しくとがっていない
- 切断時のバリ
- 切れない切断工具
- ドリルが断片を完全に通過しない
- ドリルの早期目つぶれ
- 送りが軽すぎる
- 主軸速度が速すぎる
- 冷却剤の不十分な潤滑
- テーパー穴
-
- 溶けた表面
- 刃が切れないまたはヒールのこすれ
- 不十分なサイドクリアランス
- 送り速度が遅すぎる
- 主軸速度が速すぎる
- 雑な仕上げ
- 送りが重すぎる
- 間違った逃げ角
- 工具上のとがった先端(わずかなノーズ半径が必要)
- 工具が中心に取り付けられていない
- 切断縁でのバリ
- 鋭角の角の面取りが行われていない
- 切れない工具
- 不十分なサイドクリアランス
- 工具上でリード角が指定されていない(工具は突然ではなく徐々にカットから抜ける必要がある)
- 角の亀裂または削り屑
- 工具の正レーキが大きすぎる
- 工具がゆっくりカットに入らない(突然動作に入る)
- 切れない工具
- 工具が中心より下に取り付けられている
- 工具上のとがった先端(わずかなノーズ半径が必要)
- チャッター
- 工具上のノーズ半径が大きすぎる
- 工具がしっかり取り付けられていない
- 材料が正しく支えられていない
- カット幅が広すぎる(2つのカットを使用する)
- 溶けた表面
-
- 溶けた表面
- 切れない工具
- 不十分なサイドクリアランス
- 不十分な冷却剤の供給
- 雑な仕上げ
- 送りが重すぎる
- 不適切にとがらせた工具
- 刃先が研磨されていない
- 渦巻マーク
- 後退中の工具こすれ
- 工具の先端でのバリ
- 表面の凹凸
- 先端角が大きすぎる
- 工具が主軸に対して垂直になっていない
- 工具の偏り
- 送りが重すぎる
- 工具が中心より上または下に取り付けられている
- 切断点でのニブまたはバリ
- 先端角が十分大きくない
- 切れない工具
- 送りが重すぎる
- 外径でのバリ
- 切断径内にチャンバーがない
- 切れない工具
- 溶けた表面
工作機械オペレーター用ツールキット一式のダウンロード
-
推奨される速度、ツールなど
三菱ケミカルグループ製の熱塑性樹脂製品に関する詳細 「工作機械オペレーター用ツールキット」をダウンロードしてください。この電子書籍は、さまざまな三菱ケミカルグループ製の材料に推奨される速度と工具も取り上げている、製造に関する包括的なガイドです。
-
一般的なプラスチックのマシニング加工プロセス
-
このセクションでは、プラスチックエンジニアリング部品をマシニング加工する最も一般的な方法を取り上げ、それぞれで最良の結果を達成するためのガイドラインとヒントを提供します。
適切なマシニング加工は、部品の寸法と性能を実現するために不可欠です。不適切なマシニング加工は、完成部品内に応力を生じさせ、その機械的特性に悪影響を及ぼし、早期部品故障の危険性を高める可能性があります。
マシニング加工中の応力の主な原因は次のとおりです。
• 切れない工具または設計が不適切な工具の使用
• 不適切な速度や送り量から発生した過剰な熱
• 大量の材料を取り除くマシニング加工(通常は、材料成形の片側から) -
ねじ切りとは何かねじ立てとは何か
ねじ立てとねじ切りは、ねじ山を作るために使用される2つのマシニング加工法です。ねじ切りはダイ工具を使用して雄ねじを切るプロセスであるのに対して、ねじ立てはタップ工具を使用してドリル穴の内側にねじを形成するプロセスです。
プラスチックと金属へのねじ切りとねじ立て
プラスチックをねじ切りまたはねじ立てする場合の主な考慮事項は、プラスチックは金属より切欠き脆性が高いということです。一部のポリマー材料は、特に、ファインピッチ手順においてねじ切り中に裂ける可能性があります。
プラスチックのねじ切りに関するヒント
プラスチックのねじ切りは、1点で超硬インサートを使用して行う必要があります。終点では0.001"の経路を4~5回たどります。冷却剤の使用を推奨します。
プラスチックのねじ立てに関するヒント
プラスチックをねじ立てする場合は、特定の2枚刃タップ付きのドリルを使用します。先端形成中はタップを清潔に保ちます。ねじ立て中の冷却剤使用も推奨します。
-
フライス削りとは何か
フライス削りは、固定されたプラスチック形状に高速の円筒状切削工具を当てて、軸上でカッターを移動させながらさまざまな方向に形状を削り取るマシニング加工法です。コンピュータによる数値制御(CNC)フライス削りは、プラスチックフライス削りの精度と効率性を高めます。
プラスチックと金属のフライス削り
プラスチックをフライス削りする場合は、作業台上の部品を適切に固定し、高速切削工具からの振動を最小限に抑えることが不可欠です。そうしなかった場合は、形状移動が原因のチャッターマークや精度の低下につながる可能性があります。
プラスチックのフライス削りに関するヒント
- 下向き削りとも呼ばれる下向きフライス削りは、上向きフライス削りより推奨されています。
- ミルベッド上の固定を十分に行うと、高速のテーブル移動や速い主軸速度が可能になります。
- 形状はきつく固定しすぎないようにする必要があります。変形したり、裂けたりする可能性があります。
- 正面フライス削りの場合は、正形状カッターボディを使用します。
-
のこ引きとは何か
のこ引きは、バンドソー、テーブルソー、またはその他の特化した機器を使用して材料を複数の断片に切削することを伴うマシニング加工法です。
プラスチックと金属ののこ引き
プラスチックと金属ののこ引きの主な違いは、軟化温度や融解温度が低いことが原因で、のこ刃から発生する熱がプラスチック部品に悪影響を及ぼす可能性があることです。プラスチックをのこ引きする際は、刃の速度、材料の温度特性、および形状の厚みを考慮することが不可欠です。
のこぎりの選定に関するヒント
- バンドソーは、用途が広く、直線カット、連続曲線カット、および不規則なカットに適しています。
- テーブルソーは、直線カットに適しており、複数の厚みや分厚い横断面(適切な馬力で最大4")のカットに使用できます。
のこ刃の選定に関するヒント
- 刃レーキが0°で刃セットが3~10°のリップと組み合わせ刃が、一般的なのこ引きで摩擦熱を削減するのに最適です。
- セットなしのホローグラインドされた丸のこ刃は、最大3/4"の厚みのスムーズなカットを実現します。
- 炭化タングステン刃は、耐久性があり、最適な表面仕上げを実現します。
-
穴あけとは何か穴ぐりとは何か
穴あけは、先端がとがった螺旋状工具を使用して円筒穴や通し穴を作成するマシニング加工法です。穴ぐりは、ドリル穴を広げたり、仕上げたりするための二次プロセスです。
プラスチックと金属の穴あけと穴ぐり
穴あけ操作中、特に、穴の深さが穴の直径の2倍を超える場合は、プラスチックの断熱性を考慮する必要があります。過剰な発熱は、チッピング、粗面、および不適切な許容範囲の原因になる可能性があります。
プラスチックの穴あけに関するヒント小径穴の場合(1/32”~1”)
- 普通は、高速スチールツイストドリルで十分です。
- 削り屑の除去を改善するために、頻繁な引き抜き(ペック穴あけ)を推奨します。
- スロースパイラル(ローへリックス)ドリルを使うと、削り屑の除去を改善できます。
For large diameter holes (1” and greater)
- A slow spiral (low helix) drill or general-purpose drill bit ground to a 118° point angle with 9° to 15° lip clearance is recommended. The lip rake should be ground (dubbed off) and the web thinned.
- Avoid hand feeding - drill grabbing can result in microcracks.
- It is generally best to drill a pilot hole (maximum 1/2” diameter) using 600 to 1000 rpm and a positive feed of 0.005” to 0.015” per revolution.
- Secondary drilling at 400 to 500 rpm at 0.008” to 0.020” per revolution is required to expand the hole to larger diameters.
For especially notch-sensitive materials (such as Ertalyte® PET-P and glass reinforced materials)
- A two-step process involving both drilling and boring minimizes heat build-up and reduces the risk of cracking.
- Firstdrill a 1” diameter hole using an insert drill at 500 to 800 rpm with a feed rate of 0.005” to 0.015” per revolution.
- Next bore the hole to final dimensions using a boring bar with carbide insert with 0.015” to 0.030” radii at 500 to 1000 rpm and a feed rate of 0.005” to 0.010” per revolution.
-
旋削とは何か
旋削は、プラスチック形状が固定旋盤の周りを回転するマシニング加工プロセスです。旋削は、特に、共通の回転軸に沿って対称になっている部品のマシニング加工に有用です。
プラスチックと金属の旋削
他のプラスチックマシニング加工プロセスと同様に、旋削は熱を発生させます。プラスチック部品の破損を防ぐために、材料の温度特性とともに、回転速度、工具選定、および冷却剤のすべてを慎重に検討する必要があります。
プラスチックの旋削に関するヒント
- 旋削操作には、正形状と研磨された外周を備えたインサートが必要です。
- 研磨された外周と滑らかな上面は、一般的に、インサート上の材料堆積を減らし、表面仕上げの時間を短縮します。
- 多くの場合、プラスチック旋削操作には微粒子C-2カーバイドが推奨されています。
-
-
マシニング加工でのその他の処理
-
部品やマシニング加工プロセスの要件に応じて、仕上がりを良くするために冷却剤および/または焼きなましが推奨される場合があります。このセクションでは、プラスチック部品のマシニング加工に適用可能な冷却剤と焼きなましの使用を取り上げます。
-
冷却剤とは何か
冷却剤は局所的な摩擦熱の発生を抑えるため、マシニング加工の結果が良くなり、工具の寿命が延びます。エンジニアリングプラスチックをマシニング加工する場合によく使用される冷却剤にはいくつかのタイプがあります。これには、空気、ドライアイス、スプレーミスト、および特別に開発された冷却剤が含まれます。
冷却剤が推奨される場合ほとんどのマシニング加工作業やほとんどのエンジニアリングプラスチックに冷却剤は必要ありません。ただし、次のようなケースでは冷却剤を推奨します。
- プラスチックを穴あけまたは切断する場合 - 高い摩擦熱を発生させる2つのプロセス。
- 特に切欠き脆性材料(Ertalyte™ PET-P、Duratron™ PAI、Duratron™ PBIなど)やガラス強化製品またはカーボン強化製品をマシニング加工する場合。
- 最適な表面仕上げと精密公差を達成する必要がある場合。
冷却剤の選定に関するヒント
- スプレーミストと圧縮空気は、非常に効果的な切削界面の冷却手段です。
- 汎用石油系切削液は、さまざまな金属とプラスチックに適していますが、非晶質プラスチック(Altron™ PC、Sultron™ PSU、Sultron™ PPSU、Duratron™ U1000 PEIなど)の応力亀裂の要因となる可能性があります。
- ほとんどのプラスチックに適切な冷却液はTrim E190とTim Sol LC SFの2つです。
-
アニーリングとは何か
アニーリングは、プラスチックの物理特性を向上させ、その延性を高め、その硬度を下げることによって、形状をマシニング加工しやすくする熱処理プロセスです。アニーリングは、プラスチック内部からの圧力を和らげるのに役立つため、一定期間マシニング加工する部品の寸法安定性を高めます。アニーリングプロセスには、プラスチック形状を所定の期間に融解温度の半分まで加熱することと特定の速度で冷却することが含まれます。
マシニング加工前のアニーリング
三菱ケミカルグループのアドバンスドマテリアルズ本部が提供しているすべてのプラスチック材料成形には、製造過程で発生する可能性のある内部応力を最小限に抑える独自の応力除去サイクルを使用して焼きなましを行っています。これにより、材料がマシニング加工中と加工後に寸法的に安定した状態を維持することが保証されます。
マシニング加工後のアニーリング
寸法要件や性能要件を満たすためにマシニング加工後のアニーリングを必要とするマシニング加工プラスチック部品はほとんどありませんが、マシニング加工後のアニーリングには次のようなメリットがあります。
- 耐化学性の向上 - PC、PSU、およびPEI材料は、マシニング加工後の焼きから応力クレージングを低減する恩恵を受ける可能性があります。
- 平坦性の向上と許容範囲の厳密化 - 精度平坦性と非対称コンターが必要な超精密公差部品には、マシニング加工操作中の中間焼きなましが必要な場合があります。
- 高い圧力速度と低い摩耗PAI - 高い圧力速度または可能な限り低い摩耗係数が必要な押し出しまたは射出成形Duratron™ PAI部品は、マシニング加工後のポストキュアの恩恵を受けます。このポストキュアによって、摩耗特性が最適化されます。このようなサイクルから恩恵を受けるのはPAIだけです。
プラスチックのアニーリングに関するヒント- 平坦性の向上は、粗いマシニング加工、アニーリング、および超軽切り込みによる仕上げマシニング加工によって実現可能です。
- マシニング加工中の応力の可能性を低減するには、特定の材料に関する製造ガイドラインを確認してください。材料タイプごとにガイドラインが異なることに注意してください。
- 歪みを避けるために部品が必要な形状または平面に固定されていることを確認してください。部品が全サイクルを終了し、表面が冷たくなるまで外さないでください。
- アニーリング後は、限界寸法までの仕上げマシニング加工を実施する必要があります。
- 横断面が薄い場合は、加熱時間と保持時間を変えることができます。
-
-
エンジニアリングプラスチックのトラブルシューティングに関するガイドライン
-
- テーパー穴
- 間違ってとがらせたドリル
- 不十分なクリアランス
- 送りが重すぎる
- 焼けたまたは溶けた表面
- 不正なドリルタイプ
- 間違ってとがらせたドリル
- 送りが軽すぎる
- 切れないドリル
- ウェブが厚すぎる
- 表面の削り屑
- 送りが重すぎる
- クリアランスが大きすぎる
- レーキが大きすぎる(規定された薄いウェブ)
- チャッター
- クリアランスが大きすぎる
- 送りが軽すぎる
- ドリルの突出部が大きすぎる
- レーキが大きすぎる(規定された薄いウェブ)
- 内径上の送りマークまたは渦巻線
- 送りが重すぎる
- ドリルが中心に置かれていない
- ドリルグラウンドが中心に置かれていない
- 穴が大きすぎる
- ドリルグラウンドが中心に置かれていない
- ウェブが厚すぎる
- 不十分なクリアランス
- 送り量が重すぎる
- 先端角が大きすぎる
- 穴が小さすぎる
- 切れないドリル
- クリアランスが大きすぎる
- 先端角が小さすぎる
- 穴が同心ではない
- 送りが重すぎる
- 主軸速度が遅すぎる
- 次の断片へのドリルの入りが遠すぎる
- 切断工具がニブから離れている、偏ったドリル
- ウェブが厚すぎる
- 開始時のドリル速度が重すぎる
- ドリルが中心に取り付けられていない
- ドリルが正しくとがっていない
- 切断時のバリ
- 切れない切断工具
- ドリルが断片を完全に通過しない
- ドリルの早期目つぶれ
- 送りが軽すぎる
- 主軸速度が速すぎる
- 冷却剤の不十分な潤滑
- テーパー穴
-
- 溶けた表面
- 刃が切れないまたはヒールのこすれ
- 不十分なサイドクリアランス
- 送り速度が遅すぎる
- 主軸速度が速すぎる
- 雑な仕上げ
- 送りが重すぎる
- 間違った逃げ角
- 工具上のとがった先端(わずかなノーズ半径が必要)
- 工具が中心に取り付けられていない
- 切断縁でのバリ
- 鋭角の角の面取りが行われていない
- 切れない工具
- 不十分なサイドクリアランス
- 工具上でリード角が指定されていない(工具は突然ではなく徐々にカットから抜ける必要がある)
- 角の亀裂または削り屑
- 工具の正レーキが大きすぎる
- 工具がゆっくりカットに入らない(突然動作に入る)
- 切れない工具
- 工具が中心より下に取り付けられている
- 工具上のとがった先端(わずかなノーズ半径が必要)
- チャッター
- 工具上のノーズ半径が大きすぎる
- 工具がしっかり取り付けられていない
- 材料が正しく支えられていない
- カット幅が広すぎる(2つのカットを使用する)
- 溶けた表面
-
- 溶けた表面
- 切れない工具
- 不十分なサイドクリアランス
- 不十分な冷却剤の供給
- 雑な仕上げ
- 送りが重すぎる
- 不適切にとがらせた工具
- 刃先が研磨されていない
- 渦巻マーク
- 後退中の工具こすれ
- 工具の先端でのバリ
- 表面の凹凸
- 先端角が大きすぎる
- 工具が主軸に対して垂直になっていない
- 工具の偏り
- 送りが重すぎる
- 工具が中心より上または下に取り付けられている
- 切断点でのニブまたはバリ
- 先端角が十分大きくない
- 切れない工具
- 送りが重すぎる
- 外径でのバリ
- 切断径内にチャンバーがない
- 切れない工具
- 溶けた表面
-
-
工作機械オペレーター用ツールキット一式のダウンロード
-
推奨される速度、ツールなど
三菱ケミカルグループ製の熱塑性樹脂製品に関する詳細 「工作機械オペレーター用ツールキット」をダウンロードしてください。この電子書籍は、さまざまな三菱ケミカルグループ製の材料に推奨される速度と工具も取り上げている、製造に関する包括的なガイドです。
-
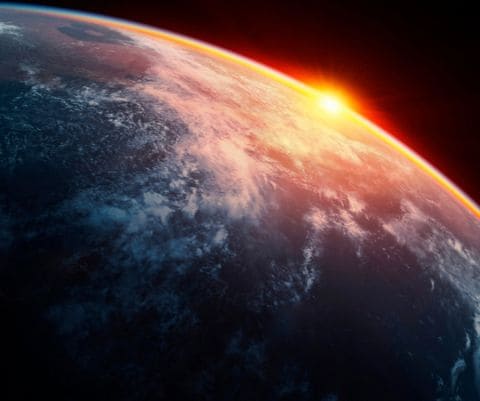