Guide d’usinage des pièces plastiques
Quelles sont les différentes méthodes d’usinage des plastiques ? Quelles spécifications doivent être prises en compte pour usiner des pièces en thermoplastique hautes performances ? Ce guide couvre les méthodes d’usinage des plastiques les plus courantes et fournit des conseils et des données utiles pour le travail des polymères techniques Mitsubishi Chemical Group.
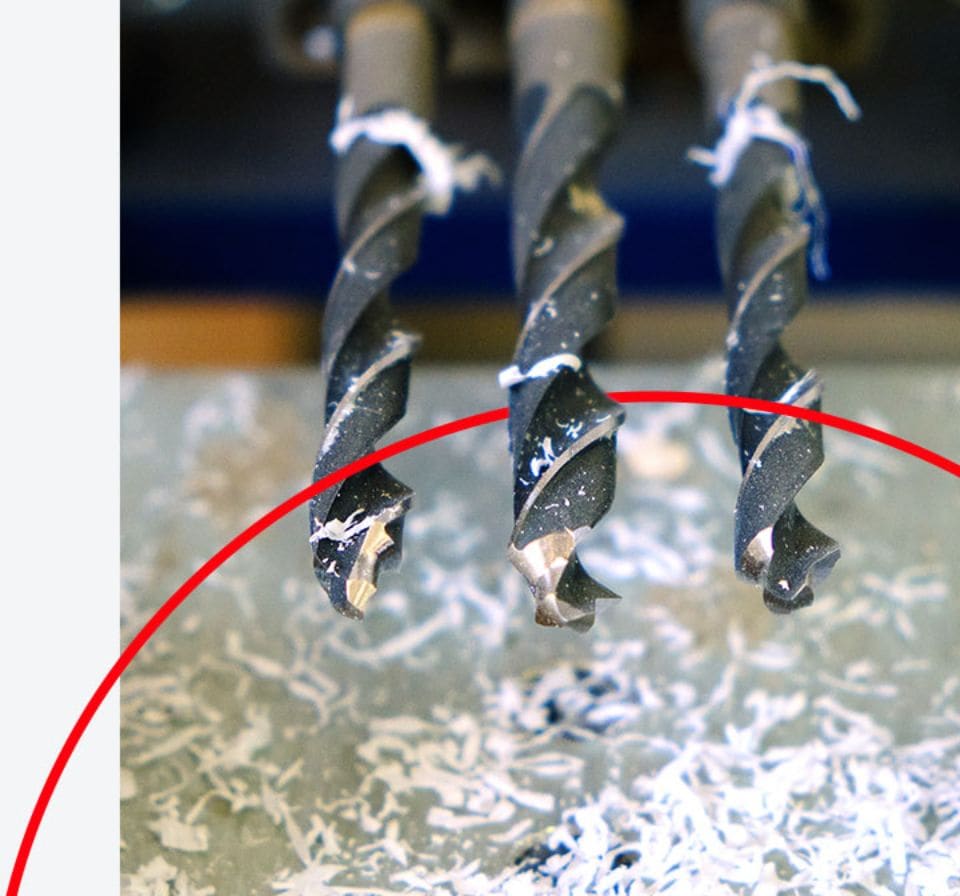
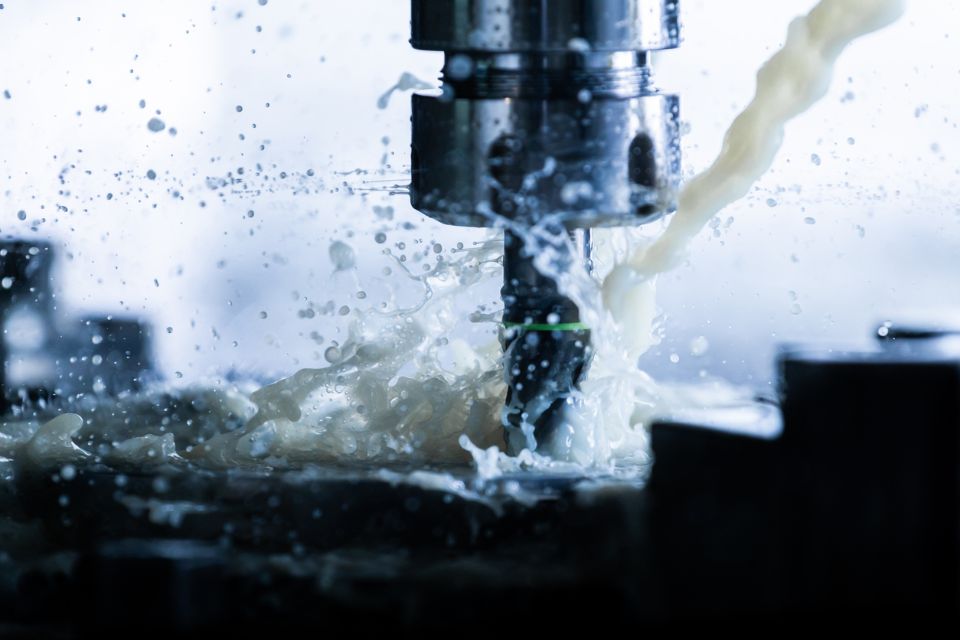
En raison de leur faible poids et de leurs propriétés mécaniques et chimiques, les plastiques remplacent de plus en plus fréquemment les métaux dans un grand nombre d’applications industrielles. De nombreuses méthodes d’usinage utilisées pour fabriquer des pièces métalliques sont adaptées à la fabrication des plastiques. Toutefois, les bonnes pratiques en la matière sont très différentes.
Les plastiques se caractérisent par diverses propriétés qui influent sur les procédures d’usinage, notamment :
- La dilatation thermique des plastiques est jusqu’à 20 fois supérieure à celle des métaux.
- La déperdition de chaleur des plastiques est plus lente que celle des métaux, ce qui accroît le risque de surchauffe localisée.
- Les températures de ramollissement et de fusion des plastiques sont bien inférieures à celles des métaux.
- Les plastiques sont bien plus élastiques que les métaux.
De la sélection des matériaux au choix de l’outillage, des vitesses d’avance aux méthodes de stabilisation, les fabricants de pièces doivent évaluer plusieurs facteurs pour obtenir de bons résultats lors de l’usinage des plastiques. Les instructions suivantes portent sur les méthodes d’usinage des plastiques les plus courantes et fournissent des conseils et des données utiles pour le travail des polymères techniques Mitsubishi Chemical Group.
Lisez la présentation ci-dessous ou téléchargez la version électronique de la boîte à outils de l’usineur, un guide complet de fabrication qui détaille, entre autres, les vitesses et outils recommandés pour divers matériaux de Mitsubishi Chemical Group.
Processus courants d’usinage des plastiques
-
Cette section traite des méthodes les plus courantes d’usinage des composants industriels plastiques, et elle fournit des instructions et des conseils qui vous permettront d’obtenir des résultats optimaux.
Un usinage approprié est essentiel pour produire des pièces présentant les dimensions et les performances voulues. Un usinage mal effectué peut entraîner une contrainte dans la pièce finie ayant pour conséquence une modification de ses propriétés mécaniques et une défaillance prématurée de la pièce.
Causes courantes génératrices de contraintes lors de l’usinage :
•Utilisation d’un outil émoussé ou mal conçu
•Chaleur excessive due à des vitesses et avances inappropriées
•Enlèvement de matière important, généralement asymétrique (un seul côté du demi-produit) -
Qu’est-ce que le filetage? Qu’est-ce que le taraudage?
Le taraudage et le filetage sont deux méthodes d’usinage utilisées pour usiner des filets. Le filetage est un processus qui consiste à utiliser une filière pour réaliser des filets externes, alors que le taraudage consiste à utiliser un outil permettant de créer des filets à l’intérieur d’un alésage (ou autre).
Filetage et taraudage du plastique par rapport au métal
La première chose à prendre en compte lors du filetage et du taraudage des plastiques, est leur sensibilité à l'entaille plus marquée que les métaux. Il y a donc un risque de rupture de filet pour certains polymères, notamment lors d'usinage au pas fin.
Conseils de filetage pour le plastique
Le filetage à un seul point du plastique doit être réalisé au tour à l’aide d’une plaquette de carbure, et quatre à cinq passes à 0,03 mm. Il est recommandé d’utiliser un fluide de refroidissement
Conseils de taraudage pour le plastique
Lors du taraudage d’une pièce en plastique, utilisez le foret spécifié avec un taraud double filet. Veillez à éviter l'accumulation de copeaux. Il est également recommandé d’utiliser un fluide de refroidissement lors du taraudage.
-
Qu’est-ce que le fraisage?
Le fraisage est une méthode d’usinage selon laquelle un outil coupant cylindrique, tournant à grande vitesse autour d’un axe dans différentes directions, est appliqué sur une pièce plastique fixe afin d’en retirer de la matière. Le fraisage à commande numérique (CNC) augmente la précision et l’efficacité du fraisage.
Fraisage du plastique comparé au métal
Lors du fraisage, il est essentiel de fixer correctement la pièce afin de réduire au maximum les vibrations générées par la grande vitesse de l’outil (risques de perte de précision, marques de broutage).
Conseils de fraisage pour le plastique
- Le fraisage en avalant est préféré au fraisage conventionnel.
- Une fixation suffisante de la matière sur la banc permet un déplacement rapide de la table et des vitesses de rotation élevées.
- La fixation ne doit toutefois pas être trop serrée, car la pièce pourrait se déformer ou sauter.
- En cas de fraisage en bout, utilisez des fraise à géométrie positive.
-
Qu’est-ce que le sciage ?
Le sciage consiste à découper un matériau en plusieurs morceaux à l’aide d’une scie à ruban, d’une scie à table ou d’un autre équipement spécialisé.
Sciage du plastique comparé au métal
La principale différence est que la chaleur générée par la lame de la scie peut avoir un impact négatif sur les pièces en plastique en raison des températures inférieures de ramollissement et de fusion de ce matériau. Lors du sciage du plastique, il est essentiel de tenir compte de la vitesse de la lame, des propriétés thermiques du matériau, et de l’épaisseur du matériau.
Conseils pour la sélection d’une scie
- Les scies à ruban sont polyvalentes et parfaitement adaptées à la réalisation de découpes droites, courbes continues ou irrégulières.
- Les scies à table conviennent aux découpes droites et permettent de couper diverses épaisseurs et des sections transversales épaisses (jusqu’à 120 mm voire plus avec la puissance appropriée).
Conseils pour la sélection d’une lame de scie
- Les lames de scie à refendre et lames à usage multiple avec angle de coupe à 0° et avec un déport de denture de 3° à 10° sont les mieux adaptées au sciage en général pour réduire la chaleur due au frottement.
- Les lames de scies circulaires à dents creuses sans jeu donneront des coupes lisses jusqu'à 19,05 mm d'épaisseur.
- Les lames au carbure de tungstène sont résistantes à l’usure et offrent des finitions de surface optimales.
-
Qu’est-ce que le perçage? Qu’est-ce que l’alésage?
Le perçage est une méthode d’usinage permettant de créer des trous cylindriques et des trous de passage à l’aide d’un outil hélicoïdal pointu. L’alésage est un processus secondaire permettant d’élargir un trou percé ou d’en effectuer la finition.
Perçage et alésage du plastique par rapport au métal
Les caractéristiques d’isolation thermique des plastiques doivent être prises en compte lors des opérations de perçage, particulièrement lorsque la profondeur du trou est deux fois supérieure à son diamètre. Une accumulation excessive de chaleur peut entraîner la formation de copeaux et de rugosités sur les surfaces, des tolérances inadéquates, voire des fissurations.
Conseils de perçage pour le plastiquePour les trous de faible diamètre (0,79 mm à 25,4 mm)
- Les forets hélicoïdaux en acier rapide sont généralement suffisants.
- Il est conseillé de procéder à de fréquents débourrages pour améliorer l’élimination des copeaux.
- Un foret à spirale lente (hélice faible) permettra de retirer plus efficacement les copeaux.
Pour les trous de grand diamètre (supérieur à 25,4 mm)
- Il est recommandé d’utiliser un foret à spirale lente (hélice faible), ou un foret à usage général affûté à un angle de pointe de 118° avec une dépouille de 9° à 15°. L’angle de coupe de la lèvre doit être affûté et l’âme doit être amincie.
- Évitez le perçage manuel : risque de micro fissures.
- Généralement il est préférable de percer un avant-trou d'un diamètre maximum de 12,7 mm avec une vitesse de 600 à 1000 tours/minute et une avance positive de 0,013 à 0,038 mm par tour.
- Pour ensuite élargir le trou à un diamètre supérieur passer à une vitesse de 400 à 500 tours/minute avec une avance de 0,02 à 0,051 mm par tour.
Pour les matériaux particulièrement sensibles à l'entaille (notamment l’Ertalyte® PET-P et les matériaux renforcés de verre)
- Un processus en deux étapes impliquant à la fois le perçage et l'alésage minimise l'accumulation de chaleur, et réduit le risque de fissuration.
- Percez d'abord un trou de 25,4 mm de diamètre à l'aide d'un foret à plaquette à 500 à 800 tr/min avec une avance de 0013 à 038 mm au tour.
- Ensuite alésez le trou aux dimensions finales à l'aide d'une barre d'alésage à plaquette carbure de rayons 0,038 à 0,077 mm à une vitesse de 500 à 1000 tours/minute, et une avance de 0,013 à 0,025 mm au tour.
-
Qu’est-ce que le tournage?
Le tournage est un processus d’usinage au cours duquel une produit plastique est soumise à une rotation sur un tour fixe. Le tournage est particulièrement utile pour l’usinage des pièces qui sont symétriques par rapport à un axe de rotation commun.
Tournage du plastique par rapport au métal
Comme les autres processus d’usinage du plastique, le tournage génère de la chaleur. Afin d’éviter d’endommager une pièce en plastique, la vitesse de rotation, le choix de l’outil et les fluides de refroidissement doivent être étudiés avec soin, ainsi que les propriétés thermiques du matériau.
Conseils de tournage pour le plastique
- Les opérations de tournage nécessitent des plaquettes avec des géométries positives et des périphéries rectifiées.
- Les périphéries rectifiées et les faces de coupe polies réduisent généralement l'accumulation de matière sur la plaquette, améliorant ainsi la finition de surface réalisable.
- Il est souvent recommandé d’utiliser un outil de coupe au carbure C-2 à grain fin pour le tournage du plastique.
Autres traitements lors de l’usinage
-
Selon les exigences de la pièce et du procédé d’usinage, des fluides de refroidissement et/ou un recuit peuvent être recommandés pour améliorer la finition. Cette section décrit l’utilisation des fluides de refroidissement et des techniques de recuit applicables à l’usinage des pièces plastiques.
-
Qu’appelle-t-on fluides de refroidissement ?
Les fluides de refroidissement réduisent l’accumulation de chaleur de frottement localisée, ce qui permet d’améliorer les résultats de l’usinage et de rallonger la durée de vie de l’outil. Plusieurs types de fluides de refroidissement sont utilisés lors de l’usinage des plastiques techniques, y compris l’air, la neige carbonique, les brouillards de vaporisation et les agents de refroidissement spécialement conçus.
Quand les fluides de refroidissement sont-ils recommandésLes fluides de refroidissement ne sont pas nécessaires pour la plupart des pratiques d’usinage et la plupart des plastiques techniques. Toutefois, nous recommandons de les utiliser dans les cas suivants :
- lors du perçage ou du tronçonnage de pièces en plastique, deux processus qui génèrent une forte chaleur de frottement.
- lors de l’usinage de matériaux particulièrement sensibles à l'entaille (Ertalyte® PET-P, Duratron® PAI, Duratron® PBI), et les produits renforcés de verre ou de carbone.
- lorsqu’il est nécessaire d’obtenir une finition optimale de la surface et de respecter des tolérances strictes.
Conseils pour la sélection d’un fluide de refroidissement
- Les brouillards de vaporisation et l’air sous pression sont des moyens très efficaces de refroidir l’outil de découpe.
- Les fluides de coupe à base de pétrole à usage général, bien qu’ils conviennent à de nombreux métaux et plastiques, peuvent contribuer à la fissuration des plastiques amorphes tels que l’Altron™ PC, le Sultron® PSU, le Sultron® PPSU et le Duratron® U1000 PEI.
- Le Trim E190 et le Tim Sol LC SF sont deux fluides de refroidissement qui conviennent à la plupart des plastiques.
-
Qu’est-ce que le recuit ?
Le recuit est un processus de traitement thermique qui améliore les propriétés physiques d'un demi-produit plastique afin qu'il soit plus facile à usiner (augmentation de la ductilité et réduction de la dureté. Cette technique permet de réduire les tensions internes du matériau, améliorant ainsi la stabilité dimensionnelle de la pièce usinée dans le temps. Le processus de recuit consiste à chauffer une demi-produit plastique à une température définie pendant une période déterminée, puis à le laisser refroidir à une vitesse donnée.
Recuit avant usinage
Tous les demi-produits plastiques de la division Advanced Materials de Mitsubishi Chemical Group sont soumis à un cycle de stabilisation exclusif et propriétaire qui réduit les contraintes internes pouvant résulter du processus de fabrication. Cette opération permet de s’assurer que le matériau restera le plus stable possible, pendant et après l’usinage.
Recuit après usinage
Peu de pièces plastiques usinées nécessitent un traitement thermique après usinage pour répondre à des exigences de dimensions ou de performances. Toutefois, ce traitement de stabilisation additionnel présente plusieurs avantages, par exemple :
- Amélioration de la résistance chimique : la stabilisation après usinage peut être utile pour réduire les fissurations pouvant apparaître sur les matériaux amorphes (PC, PSU et PEI).
- Amélioration de la planéité, tolérances plus serrées : les pièces avec des tolérances très serrées nécessitant un bonne planéité et/ou des formes asymétriques, doivent dans certains cas faire l’objet d’un recuit intermédiaire entre les opérations d’usinage.
- Les pièces en Duratron® PAI , extrudé ou injecté , nécessitant des limites "Pression-Vitesse" élevées, et le plus faible taux d’usure possible, peuvent bénéficier avantageusement d'un recuit supplémentaire après usinage qui optimisera ces performances en augmentant la tenue à l'usure. Ce cycle ne présente des avantages que pour le PAI.
Conseils pour le recuit des plastiques- La meilleure planéité est obtenue suivant la chronologie ébauchage, recuit, puis passes de finition.
- Consulter les consignes relatives à la fabrication du matériau concerné pour limiter les risques liés à la relaxation des contraintes lors de l’usinage. Noter que ces consignes varient en fonction du type de matériau.
- Vérifier que les pièces soient correctement fixées afin d’éviter toute déformation ; pas de démontage des pièces tant que le cycle n’est pas terminé et qu’elles ne sont pas froides au toucher.
- L’usinage de finition permettant d’obtenir les dimensions finales souhaitées doit être effectué après le recuit.
- La montée en température et la durée de maintien peuvent changer si les sections transversales sont fines.
Conseils de dépannage pour les plastiques techniques
-
- Trou conique
- Foret mal affûté
- Jeu insuffisant
- Avance trop importante
- Surface brûlée ou fondue
- Type de foret incorrect
- Foret mal affûté
- Avance insuffisante
- Foret émoussé
- Âme trop épaisse
- Copeaux en surface
- Avance trop importante
- Dépouille trop forte
- Angle de coupe trop important (âme fine)
- Broutage
- Dépouille trop forte
- Avance insuffisante
- Trop forte inclinaison du foret
- Angle de coupe trop important (âme fine)
- Marques de l’avance ou lignes hélicoïdales sur le diamètre intérieur
- Avance trop importante
- Foret non centré
- Affûtage du foret non centré
- Trous surdimensionnés
- Affûtage du foret non centré
- Âme trop épaisse
- jeu insuffisant
- Avance trop rapide
- Angle de pointe trop important
- Trous sous-dimensionnés
- Foret émoussé
- Dépouille trop importante
- Angle de pointe trop faible
- Trous non concentriques
- Avance trop importante
- Vitesse de la broche trop faible
- Le foret entre trop vite dans la pièce suivante
- L’outil de découpe laisse des aspérités, le foret dévie
- Âme trop épaisse
- Vitesse du foret trop importante au démarrage
- Foret non centré
- Foret mal affûté
- Bavure lors de la découpe
- Outil de découpe émoussé
- Le foret ne passe pas complètement à travers la pièce
- Le foret s’émousse rapidement
- Avance insuffisante
- Vitesse de la broche trop élevée
- Graissage par le fluide de refroidissement insuffisant
- Trou conique
-
- Surface fondue
- Outil trop émoussé ou frottement du talon
- Dépouille latérale insuffisante
- Avance trop lente
- Vitesse de la broche trop élevée
- Finition rugueuse
- Avance trop importante
- Angles de dépouille incorrects
- Pointe acérée sur l’outil (léger arrondi de bec nécessaire)
- L’outil n’est pas monté au centre
- Bavures au bord de la coupure
- Absence de chanfrein aux angles vifs
- Outil émoussé
- Dépouille latérale insuffisante
- Pas d'angle d’attaque sur l’outil (l’outil doit s’arrêter de couper progressivement, pas subitement)
- Fissures ou copeaux au niveau des angles
- L’angle de coupe positif de l’outil est trop important
- L’outil commence trop brusquement à couper
- Outil émoussé
- Outil monté sous le centre
- Pointe acérée sur l’outil (léger arrondi de bec nécessaire)
- Broutage
- Arrondi du bec de l’outil trop important
- L’outil n’est pas monté solidement
- Le matériau n’est pas correctement soutenu
- Largeur de coupe trop importante (utiliser deux coupes)
- Surface fondue
-
- Surface fondue
- Outil émoussé
- Dépouille latérale insuffisante
- Quantité de fluide de refroidissement insuffisante
- Finition rugueuse
- Avance trop importante
- Outil mal affûté
- Arête de coupe non aiguisée
- Marques hélicoïdales
- L’outil frotte lors de son retrait
- Bavure à la pointe de l’outil
- Surfaces concaves ou convexes
- Angle de pointe trop important
- Outil non perpendiculaire à la broche
- Déviation de l’outil
- Avance trop importante
- Outil monté au-dessus ou au-dessous du centre
- Aspérités ou bavures au point de découpe
- Angle de pointe pas assez grand
- Outil émoussé
- Avance trop importante
- Bavures sur le diamètre extérieur
- Pas de chambre avant le diamètre de découpe
- Outil émoussé
- Surface fondue
Téléchargez l’intégralité de la Boîte à outils de l’usineur
-
VITESSES RECOMMANDÉES, OUTILS ET PLUS
D'avantage d'informations sur nos thermoplastiques Téléchargez notre version numérique du guide de l'usinage (machinist's Toolkit), une aide complète à la fabrication avec les vitesses et les outils recommandés pour la gamme de matériaux Mitsubishi Chemical Group.
-
Processus courants d’usinage des plastiques
-
Cette section traite des méthodes les plus courantes d’usinage des composants industriels plastiques, et elle fournit des instructions et des conseils qui vous permettront d’obtenir des résultats optimaux.
Un usinage approprié est essentiel pour produire des pièces présentant les dimensions et les performances voulues. Un usinage mal effectué peut entraîner une contrainte dans la pièce finie ayant pour conséquence une modification de ses propriétés mécaniques et une défaillance prématurée de la pièce.
Causes courantes génératrices de contraintes lors de l’usinage :
•Utilisation d’un outil émoussé ou mal conçu
•Chaleur excessive due à des vitesses et avances inappropriées
•Enlèvement de matière important, généralement asymétrique (un seul côté du demi-produit) -
Qu’est-ce que le filetage? Qu’est-ce que le taraudage?
Le taraudage et le filetage sont deux méthodes d’usinage utilisées pour usiner des filets. Le filetage est un processus qui consiste à utiliser une filière pour réaliser des filets externes, alors que le taraudage consiste à utiliser un outil permettant de créer des filets à l’intérieur d’un alésage (ou autre).
Filetage et taraudage du plastique par rapport au métal
La première chose à prendre en compte lors du filetage et du taraudage des plastiques, est leur sensibilité à l'entaille plus marquée que les métaux. Il y a donc un risque de rupture de filet pour certains polymères, notamment lors d'usinage au pas fin.
Conseils de filetage pour le plastique
Le filetage à un seul point du plastique doit être réalisé au tour à l’aide d’une plaquette de carbure, et quatre à cinq passes à 0,03 mm. Il est recommandé d’utiliser un fluide de refroidissement
Conseils de taraudage pour le plastique
Lors du taraudage d’une pièce en plastique, utilisez le foret spécifié avec un taraud double filet. Veillez à éviter l'accumulation de copeaux. Il est également recommandé d’utiliser un fluide de refroidissement lors du taraudage.
-
Qu’est-ce que le fraisage?
Le fraisage est une méthode d’usinage selon laquelle un outil coupant cylindrique, tournant à grande vitesse autour d’un axe dans différentes directions, est appliqué sur une pièce plastique fixe afin d’en retirer de la matière. Le fraisage à commande numérique (CNC) augmente la précision et l’efficacité du fraisage.
Fraisage du plastique comparé au métal
Lors du fraisage, il est essentiel de fixer correctement la pièce afin de réduire au maximum les vibrations générées par la grande vitesse de l’outil (risques de perte de précision, marques de broutage).
Conseils de fraisage pour le plastique
- Le fraisage en avalant est préféré au fraisage conventionnel.
- Une fixation suffisante de la matière sur la banc permet un déplacement rapide de la table et des vitesses de rotation élevées.
- La fixation ne doit toutefois pas être trop serrée, car la pièce pourrait se déformer ou sauter.
- En cas de fraisage en bout, utilisez des fraise à géométrie positive.
-
Qu’est-ce que le sciage ?
Le sciage consiste à découper un matériau en plusieurs morceaux à l’aide d’une scie à ruban, d’une scie à table ou d’un autre équipement spécialisé.
Sciage du plastique comparé au métal
La principale différence est que la chaleur générée par la lame de la scie peut avoir un impact négatif sur les pièces en plastique en raison des températures inférieures de ramollissement et de fusion de ce matériau. Lors du sciage du plastique, il est essentiel de tenir compte de la vitesse de la lame, des propriétés thermiques du matériau, et de l’épaisseur du matériau.
Conseils pour la sélection d’une scie
- Les scies à ruban sont polyvalentes et parfaitement adaptées à la réalisation de découpes droites, courbes continues ou irrégulières.
- Les scies à table conviennent aux découpes droites et permettent de couper diverses épaisseurs et des sections transversales épaisses (jusqu’à 120 mm voire plus avec la puissance appropriée).
Conseils pour la sélection d’une lame de scie
- Les lames de scie à refendre et lames à usage multiple avec angle de coupe à 0° et avec un déport de denture de 3° à 10° sont les mieux adaptées au sciage en général pour réduire la chaleur due au frottement.
- Les lames de scies circulaires à dents creuses sans jeu donneront des coupes lisses jusqu'à 19,05 mm d'épaisseur.
- Les lames au carbure de tungstène sont résistantes à l’usure et offrent des finitions de surface optimales.
-
Qu’est-ce que le perçage? Qu’est-ce que l’alésage?
Le perçage est une méthode d’usinage permettant de créer des trous cylindriques et des trous de passage à l’aide d’un outil hélicoïdal pointu. L’alésage est un processus secondaire permettant d’élargir un trou percé ou d’en effectuer la finition.
Perçage et alésage du plastique par rapport au métal
Les caractéristiques d’isolation thermique des plastiques doivent être prises en compte lors des opérations de perçage, particulièrement lorsque la profondeur du trou est deux fois supérieure à son diamètre. Une accumulation excessive de chaleur peut entraîner la formation de copeaux et de rugosités sur les surfaces, des tolérances inadéquates, voire des fissurations.
Conseils de perçage pour le plastiquePour les trous de faible diamètre (0,79 mm à 25,4 mm)
- Les forets hélicoïdaux en acier rapide sont généralement suffisants.
- Il est conseillé de procéder à de fréquents débourrages pour améliorer l’élimination des copeaux.
- Un foret à spirale lente (hélice faible) permettra de retirer plus efficacement les copeaux.
Pour les trous de grand diamètre (supérieur à 25,4 mm)
- Il est recommandé d’utiliser un foret à spirale lente (hélice faible), ou un foret à usage général affûté à un angle de pointe de 118° avec une dépouille de 9° à 15°. L’angle de coupe de la lèvre doit être affûté et l’âme doit être amincie.
- Évitez le perçage manuel : risque de micro fissures.
- Généralement il est préférable de percer un avant-trou d'un diamètre maximum de 12,7 mm avec une vitesse de 600 à 1000 tours/minute et une avance positive de 0,013 à 0,038 mm par tour.
- Pour ensuite élargir le trou à un diamètre supérieur passer à une vitesse de 400 à 500 tours/minute avec une avance de 0,02 à 0,051 mm par tour.
Pour les matériaux particulièrement sensibles à l'entaille (notamment l’Ertalyte® PET-P et les matériaux renforcés de verre)
- Un processus en deux étapes impliquant à la fois le perçage et l'alésage minimise l'accumulation de chaleur, et réduit le risque de fissuration.
- Percez d'abord un trou de 25,4 mm de diamètre à l'aide d'un foret à plaquette à 500 à 800 tr/min avec une avance de 0013 à 038 mm au tour.
- Ensuite alésez le trou aux dimensions finales à l'aide d'une barre d'alésage à plaquette carbure de rayons 0,038 à 0,077 mm à une vitesse de 500 à 1000 tours/minute, et une avance de 0,013 à 0,025 mm au tour.
-
Qu’est-ce que le tournage?
Le tournage est un processus d’usinage au cours duquel une produit plastique est soumise à une rotation sur un tour fixe. Le tournage est particulièrement utile pour l’usinage des pièces qui sont symétriques par rapport à un axe de rotation commun.
Tournage du plastique par rapport au métal
Comme les autres processus d’usinage du plastique, le tournage génère de la chaleur. Afin d’éviter d’endommager une pièce en plastique, la vitesse de rotation, le choix de l’outil et les fluides de refroidissement doivent être étudiés avec soin, ainsi que les propriétés thermiques du matériau.
Conseils de tournage pour le plastique
- Les opérations de tournage nécessitent des plaquettes avec des géométries positives et des périphéries rectifiées.
- Les périphéries rectifiées et les faces de coupe polies réduisent généralement l'accumulation de matière sur la plaquette, améliorant ainsi la finition de surface réalisable.
- Il est souvent recommandé d’utiliser un outil de coupe au carbure C-2 à grain fin pour le tournage du plastique.
-
-
Autres traitements lors de l’usinage
-
Selon les exigences de la pièce et du procédé d’usinage, des fluides de refroidissement et/ou un recuit peuvent être recommandés pour améliorer la finition. Cette section décrit l’utilisation des fluides de refroidissement et des techniques de recuit applicables à l’usinage des pièces plastiques.
-
Qu’appelle-t-on fluides de refroidissement ?
Les fluides de refroidissement réduisent l’accumulation de chaleur de frottement localisée, ce qui permet d’améliorer les résultats de l’usinage et de rallonger la durée de vie de l’outil. Plusieurs types de fluides de refroidissement sont utilisés lors de l’usinage des plastiques techniques, y compris l’air, la neige carbonique, les brouillards de vaporisation et les agents de refroidissement spécialement conçus.
Quand les fluides de refroidissement sont-ils recommandésLes fluides de refroidissement ne sont pas nécessaires pour la plupart des pratiques d’usinage et la plupart des plastiques techniques. Toutefois, nous recommandons de les utiliser dans les cas suivants :
- lors du perçage ou du tronçonnage de pièces en plastique, deux processus qui génèrent une forte chaleur de frottement.
- lors de l’usinage de matériaux particulièrement sensibles à l'entaille (Ertalyte® PET-P, Duratron® PAI, Duratron® PBI), et les produits renforcés de verre ou de carbone.
- lorsqu’il est nécessaire d’obtenir une finition optimale de la surface et de respecter des tolérances strictes.
Conseils pour la sélection d’un fluide de refroidissement
- Les brouillards de vaporisation et l’air sous pression sont des moyens très efficaces de refroidir l’outil de découpe.
- Les fluides de coupe à base de pétrole à usage général, bien qu’ils conviennent à de nombreux métaux et plastiques, peuvent contribuer à la fissuration des plastiques amorphes tels que l’Altron™ PC, le Sultron® PSU, le Sultron® PPSU et le Duratron® U1000 PEI.
- Le Trim E190 et le Tim Sol LC SF sont deux fluides de refroidissement qui conviennent à la plupart des plastiques.
-
Qu’est-ce que le recuit ?
Le recuit est un processus de traitement thermique qui améliore les propriétés physiques d'un demi-produit plastique afin qu'il soit plus facile à usiner (augmentation de la ductilité et réduction de la dureté. Cette technique permet de réduire les tensions internes du matériau, améliorant ainsi la stabilité dimensionnelle de la pièce usinée dans le temps. Le processus de recuit consiste à chauffer une demi-produit plastique à une température définie pendant une période déterminée, puis à le laisser refroidir à une vitesse donnée.
Recuit avant usinage
Tous les demi-produits plastiques de la division Advanced Materials de Mitsubishi Chemical Group sont soumis à un cycle de stabilisation exclusif et propriétaire qui réduit les contraintes internes pouvant résulter du processus de fabrication. Cette opération permet de s’assurer que le matériau restera le plus stable possible, pendant et après l’usinage.
Recuit après usinage
Peu de pièces plastiques usinées nécessitent un traitement thermique après usinage pour répondre à des exigences de dimensions ou de performances. Toutefois, ce traitement de stabilisation additionnel présente plusieurs avantages, par exemple :
- Amélioration de la résistance chimique : la stabilisation après usinage peut être utile pour réduire les fissurations pouvant apparaître sur les matériaux amorphes (PC, PSU et PEI).
- Amélioration de la planéité, tolérances plus serrées : les pièces avec des tolérances très serrées nécessitant un bonne planéité et/ou des formes asymétriques, doivent dans certains cas faire l’objet d’un recuit intermédiaire entre les opérations d’usinage.
- Les pièces en Duratron® PAI , extrudé ou injecté , nécessitant des limites "Pression-Vitesse" élevées, et le plus faible taux d’usure possible, peuvent bénéficier avantageusement d'un recuit supplémentaire après usinage qui optimisera ces performances en augmentant la tenue à l'usure. Ce cycle ne présente des avantages que pour le PAI.
Conseils pour le recuit des plastiques- La meilleure planéité est obtenue suivant la chronologie ébauchage, recuit, puis passes de finition.
- Consulter les consignes relatives à la fabrication du matériau concerné pour limiter les risques liés à la relaxation des contraintes lors de l’usinage. Noter que ces consignes varient en fonction du type de matériau.
- Vérifier que les pièces soient correctement fixées afin d’éviter toute déformation ; pas de démontage des pièces tant que le cycle n’est pas terminé et qu’elles ne sont pas froides au toucher.
- L’usinage de finition permettant d’obtenir les dimensions finales souhaitées doit être effectué après le recuit.
- La montée en température et la durée de maintien peuvent changer si les sections transversales sont fines.
-
-
Conseils de dépannage pour les plastiques techniques
-
- Trou conique
- Foret mal affûté
- Jeu insuffisant
- Avance trop importante
- Surface brûlée ou fondue
- Type de foret incorrect
- Foret mal affûté
- Avance insuffisante
- Foret émoussé
- Âme trop épaisse
- Copeaux en surface
- Avance trop importante
- Dépouille trop forte
- Angle de coupe trop important (âme fine)
- Broutage
- Dépouille trop forte
- Avance insuffisante
- Trop forte inclinaison du foret
- Angle de coupe trop important (âme fine)
- Marques de l’avance ou lignes hélicoïdales sur le diamètre intérieur
- Avance trop importante
- Foret non centré
- Affûtage du foret non centré
- Trous surdimensionnés
- Affûtage du foret non centré
- Âme trop épaisse
- jeu insuffisant
- Avance trop rapide
- Angle de pointe trop important
- Trous sous-dimensionnés
- Foret émoussé
- Dépouille trop importante
- Angle de pointe trop faible
- Trous non concentriques
- Avance trop importante
- Vitesse de la broche trop faible
- Le foret entre trop vite dans la pièce suivante
- L’outil de découpe laisse des aspérités, le foret dévie
- Âme trop épaisse
- Vitesse du foret trop importante au démarrage
- Foret non centré
- Foret mal affûté
- Bavure lors de la découpe
- Outil de découpe émoussé
- Le foret ne passe pas complètement à travers la pièce
- Le foret s’émousse rapidement
- Avance insuffisante
- Vitesse de la broche trop élevée
- Graissage par le fluide de refroidissement insuffisant
- Trou conique
-
- Surface fondue
- Outil trop émoussé ou frottement du talon
- Dépouille latérale insuffisante
- Avance trop lente
- Vitesse de la broche trop élevée
- Finition rugueuse
- Avance trop importante
- Angles de dépouille incorrects
- Pointe acérée sur l’outil (léger arrondi de bec nécessaire)
- L’outil n’est pas monté au centre
- Bavures au bord de la coupure
- Absence de chanfrein aux angles vifs
- Outil émoussé
- Dépouille latérale insuffisante
- Pas d'angle d’attaque sur l’outil (l’outil doit s’arrêter de couper progressivement, pas subitement)
- Fissures ou copeaux au niveau des angles
- L’angle de coupe positif de l’outil est trop important
- L’outil commence trop brusquement à couper
- Outil émoussé
- Outil monté sous le centre
- Pointe acérée sur l’outil (léger arrondi de bec nécessaire)
- Broutage
- Arrondi du bec de l’outil trop important
- L’outil n’est pas monté solidement
- Le matériau n’est pas correctement soutenu
- Largeur de coupe trop importante (utiliser deux coupes)
- Surface fondue
-
- Surface fondue
- Outil émoussé
- Dépouille latérale insuffisante
- Quantité de fluide de refroidissement insuffisante
- Finition rugueuse
- Avance trop importante
- Outil mal affûté
- Arête de coupe non aiguisée
- Marques hélicoïdales
- L’outil frotte lors de son retrait
- Bavure à la pointe de l’outil
- Surfaces concaves ou convexes
- Angle de pointe trop important
- Outil non perpendiculaire à la broche
- Déviation de l’outil
- Avance trop importante
- Outil monté au-dessus ou au-dessous du centre
- Aspérités ou bavures au point de découpe
- Angle de pointe pas assez grand
- Outil émoussé
- Avance trop importante
- Bavures sur le diamètre extérieur
- Pas de chambre avant le diamètre de découpe
- Outil émoussé
- Surface fondue
-
-
Téléchargez l’intégralité de la Boîte à outils de l’usineur
-
VITESSES RECOMMANDÉES, OUTILS ET PLUS
D'avantage d'informations sur nos thermoplastiques Téléchargez notre version numérique du guide de l'usinage (machinist's Toolkit), une aide complète à la fabrication avec les vitesses et les outils recommandés pour la gamme de matériaux Mitsubishi Chemical Group.
-
Contactez notre équipe de spécialistes en remplissant le formulaire de contact. Nous sommes prêts à relever votre prochain défi.
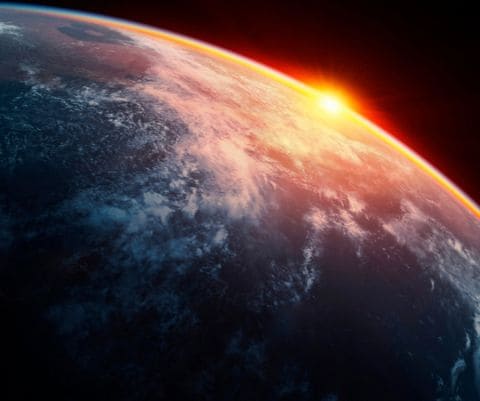