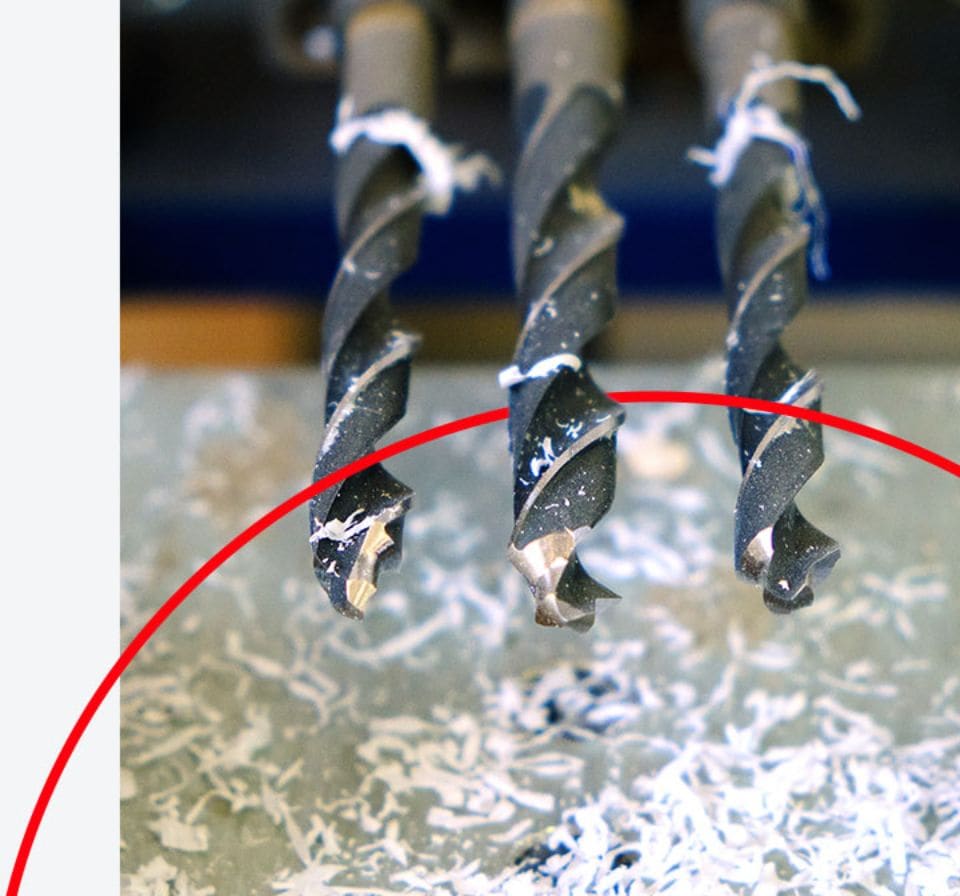
塑料凭借其优越的机械、化学和轻质属性,在各式各样的工程应用中日渐取代金属。许多用于制造金属零件的加工方法同样也用于塑料。但加工塑料的最佳方法却大为不同。
塑料展现出许多会影响加工程序的性能,包括:
- 塑料热膨胀比金属大 10 倍之多
- 塑料散热比金属更慢,增加了局部过热的风险
- 塑料的软化和熔化温度比金属低得多
- 塑料弹性比金属大得多
从材料选择到正确工具,从进给速率到固定方法,在加工塑料时,零件生产商必须权衡各种因素,以便获得良好结果。以下指南涵盖了最常用的塑料加工方法,并提供了来自 Mitsubishi Chemical Group 的用于加工塑料的实用技巧和数据。
阅读以下概述或下载机械师手册电子书,这是完整的制造指南,涵盖适用于 Mitsubishi Chemical Group 一系列材料的建议速度和工具。
常用塑料加工工艺
-
此部分涵盖了最常用的塑料工程部件加工方法,为每一种部件都提供了获得最佳加工结果的指南和技巧。
正确加工对于到达零件尺寸要求和实现零件性能至关重要。加工不当会使完工零件产生应力,对其机械性能造成负面影响,且零件有提前失效的风险。
常见机械加工残余应力成因包括:
• 使用钝化或选型不当的刀具
• 转速和进给速率不当所产生的过多热量
• 通过加工去掉大量材料,通常是从型材一侧 -
何为车螺纹?何为攻丝?
车螺纹和攻丝是用于生产螺纹的两种加工方法。车螺纹是用板牙切出外螺纹的过程,而攻丝则是用丝攻在已钻好的孔内加工出螺纹的过程。
对塑料与金属进行车螺纹和攻丝对比
对塑料材料车螺纹和攻丝时的一个主要考量因素为,塑料比金属对缺口更敏感。在车螺纹过程中,尤其是在细牙加工程序中,一些聚合物材料可能会开裂
塑料的车螺纹加工技巧
需用硬质合金刀片在单个点上进行塑料车螺纹加工,结束时进行四到五次加工精度为 0.001" 走刀。建议使用冷却剂。
塑料的攻丝加工技巧
对塑料进行攻丝加工时,需使用特定的双槽丝攻。保持丝攻内无碎屑聚集。在攻丝过程中同样建议使用冷却剂。
-
何为铣削?
铣削是一种在静止塑料型材上使用高速圆柱形切割刀具进行加工的方法,铣削时,沿轴移动刀具以便从不同方向削除型材上的材料。计算机数字控制 (CNC) 铣削能改善塑料铣削的精度和效率。
塑料与金属的铣削对比
在铣削塑料时,至关重要的一点是将零件正确固定在工作台上,并将来自高速刀具的振动降至最低,否则可能会使型材移位,进而导致颤纹并降低精度。
塑料的铣削技巧
- 建议使用顺铣,又名同向铣削,而非传统铣削。
- 在铣床床身上进行充分固定,能实现工作台快速移动和主轴高速旋转。
- 当然,也不应将型材固定得太紧,因其可能会变形或回弹。
- 端面铣削时,请使用正几何形状刀体。
-
何为锯切?
锯切是一种用带锯、台锯或其他专用设备将材料切割成多个小块的加工方法。
塑料与金属的锯切对比
塑料与金属锯切之间的主要不同点在于,锯片所产生的热量会对塑料零件造成负面影响,因其软化和熔化温度更低。至关重要的一点是,在锯切塑料时考虑锯片速度、材料热属性以及型材厚度。
锯切刀具选择技巧
- 带锯应用场景广泛,用于直线、连续曲线以及不规则切割时效果很好。
- 对于直线切割,台锯很方便,且其具备足够马力,能用于切割多种厚度和较厚横截面(最厚可达 4")。
锯片选择技巧
- 具备 0° 锯齿前倾角以及 3° 至 10° 锯齿组的直锯和组合锯是普通锯切的上佳之选,这可以减少摩擦生热。
- 无胶凹磨圆锯片会产生厚达 3/4" 的光滑切口。
- 钨钢刀片耐磨且能实现优质表面光洁度。
-
何为钻孔?何为镗孔?
钻孔是一种利用尖头螺旋刀具生成圆柱形孔和通孔的加工方法。镗孔是一种将已钻好的孔加大或精加工的精加工工艺。
塑料与金属的钻孔对比
在钻孔操作过程中需考量塑料隔热特性,当孔深大于两倍孔径时尤其如此。过多热量聚集可能会导致剥落、表面粗糙和误差过大。
塑料钻孔技巧对于小孔径(1/32" 至 1")
- 高速钢制麻花钻头通常就已足够。
- 建议频繁退出(啄式钻孔)以促进排屑。
- 平螺旋(低螺旋线)钻头能更好地排屑。
对于大孔径(大于等于25.400 mm)
- 建议使用平螺旋(低螺旋线)钻头或打磨至顶角118°且钻刃余隙为9°至15°的通用型钻头。应打磨(锐化)钻刃前刀面并磨薄钻心。
- 避免手动进给,因为钻头夹紧机构可能会导致微裂纹。
- 通常,最好先用600至1000 rpm以及每转0.127 mm至0.381 mm的正进给钻一个导向孔(直径最大12.700 mm)。
- 需要用400至500 rpm以及每转0.203 mm至0.508 mm的进给来二次钻孔以扩大孔径。
对于缺口敏感性极强的材料(如 Ertalyte® PET-P和玻璃纤维增强材料)
- 包含钻孔和镗孔的两步骤工艺能将热聚集最小化并减小裂纹风险。
- 首先,用刀片钻头以500至800 rpm以及每转0.127 mm至0.381 mm的进给速率钻一个直径为25.400 mm的孔。
- 接着,用配有半径为0.381 mm至0.762 mm硬质合金刀片的镗杆以500至1000 rpm以及每转0.127 mm至0.254 mm的进给速率来将孔镗至最终尺寸。
-
何为车削?
车削是一种塑料型材围绕静止车床旋转的加工工艺。对于沿共同旋转轴对称的加工零件,车削尤其有用。
塑料与金属的车削对比
与其他塑料加工工艺一样,车削也会产生热量。为了防止塑料件受损,材料热性能以及转速、刀具选择和冷却剂的使用都需仔细考量。
塑料车削技巧
- 车削操作需要具用正几何形状以及已打磨周边的刀片。
- 已打磨周边和已抛光顶面通常能减少刀片上的材料聚集,实现更优的表面光洁度。
- 通常建议将细晶粒 C-2 硬质合金刀具用于塑料车削操作。
额外加工处理
-
取决于零件和加工工艺要求,可建议使用冷却剂和/或退火以改善成品效果。本节介绍适用于加工塑料零件的冷却剂和退火工艺。
-
何为冷却剂?
冷却剂能减少局部摩擦热量聚集,从而改善加工结果并延长刀具寿命。在加工工程塑料时常用的冷却剂有很多种,包括空气、干冰、喷雾以及专门开发的冷却剂。
何时建议使用冷却剂?大多数加工操作以及大多数工程塑料并不需要冷却剂。尽管如此,以下情况下仍建议使用冷却剂:
- 在对塑料进行钻孔或切割时,因为这两种工艺会产生大量摩擦热。
- 在加工缺口敏感性极强的材料时,如 Ertalyte® PET-P、Duratron® PAI、Duratron® PBI 和玻璃纤维或碳纤维增强产品。
- 为实现优质表面光洁度和窄误差而有必要时。
冷却剂选择技巧
- 喷雾和压缩气体是冷却切割界面非常有效的方法。
- 虽然通用型石油基切削液适用于许多金属和塑料,但可能导致无定形塑料应力开裂,如 Altron™ PC、Sultron® PSU、Sultron® PPSU 和 Duratron® U1000 PEI。
- 适用于大多数塑料的两种射流冷却剂为 Trim E190 和 Tim Sol LC SF。
-
何为退火?
退火是一种热处理工艺,能改善塑料的物理性能,增加其延展性并减少其硬度,使型材更易于加工。退火有助于释放塑料内应力,赋予已加工零件更高的长期尺寸稳定性。退火工艺要求将塑料型材加热至其熔化温度的二分之一并保持既定时长,然后让其以特定速度冷却。
加工前退火
来自 Mitsubishi Chemical Group“先进材料”部门的所有塑料型材均已用专利去应力循环来退火,该循环能将所有可能由制造工艺所导致的内部应力最小化。这能确保材料尺寸在加工过程中以及加工后保持稳定。
加工后退火
鲜有已加工塑料零件需要在加工后进行退火以满足尺寸或性能要求;尽管如此,加工后退火确实有若干益处,包括:
- 提升耐化学性 – PC、PSU 和 PEI 材料能从加工后退火中获益,减少应力龟裂。
- 获得更佳平直度和更窄误差 – 要求精确平直度和非对称轮廓的极窄误差零件有时需要在加工操作之间进行工序间退火。
- 高压力速度和低磨损 PAI -要求高压力速度或尽可能低磨损系数的挤出或注塑成形 Duratron® PAI 零件能从加工后的额外固化中获益。此固化工艺能优化耐磨性能。只有 PAI 能从此循环中获益。
塑料退火技巧- 通过粗加工、退火和用非常小的切削量来精加工,可实现更好的平直度。
- 为减少潜在的加工所致应力,请查看特定材料的制造指南。请注意,指南会随材料类型的变化而变化。
- 确保已用夹具将零件固定至所需形状或平直度以防止变形。在零件已完成整个循环且触摸时感觉不热之后,才能松开零件。
- 退火之后应进行精加工,以达到关键尺寸要求。
- 若横截面较薄,则可更改加热和保温时间。
工程塑料排障指南
-
- 锥形孔
- 钻头刃磨不当
- 间隙不足
- 进给太大
- 表面烧蚀或熔化
- 钻头类型错误
- 钻头刃磨不当
- 进给太小
- 钻头不锋利
- 钻心太厚
- 表面剥落
- 进给太大
- 间隙太大
- 前刀面太大(表述为钻心偏薄)
- 振刀
- 间隙太大
- 进给太小
- 钻头伸出过长
- 前刀面太大(表述为钻心偏薄)
- 内径有进给痕或螺旋线
- 进给太大
- 钻头未对中
- 钻头打磨未对中
- 孔径过大
- 钻头打磨未对中
- 钻心太厚
- 间隙不足
- 进给速率太快
- 顶尖角太大
- 孔径过小
- 钻头不锋利
- 间隙太大
- 顶尖角太小
- 孔不同心
- 进给太大
- 主轴转速太慢
- 钻头钻入下一工件太深
- 切削刀具留下的尖刺使钻头偏向
- 钻心太厚
- 钻头起始转速太快
- 钻头未装在中心位置
- 钻头刃磨不当
- 切削毛刺
- 切削刀具不锋利
- 钻头未完全穿过工件
- 钻头迅速变钝
- 进给太小
- 主轴转速太快
- 冷却剂润滑不足
- 锥形孔
-
- 表面熔化
- 太钝或后棱摩擦
- 侧隙不足
- 进给速率太慢
- 主轴转速太快
- 粗加工面
- 进给太大
- 间隙角错误
- 刀具刀尖过于尖锐(要求刀尖稍微倒圆)
- 刀具未装在中心位置
- 切削边缘毛刺
- 尖锐角未倒角
- 刀具不锋利
- 侧隙不足
- 刀具上无导程角(刀具应逐步而非突然从切削处退出)
- 角落处裂纹或剥落
- 刀具正前刀面太大
- 刀尖并非慢慢切入
- 刀具不锋利
- 刀具安装在中心之下
- 刀具刀尖过于尖锐(要求刀尖稍微倒圆)
- 振刀
- 刀尖倒圆半径太大
- 刀具未安装牢固
- 材料支撑不当
- 切削宽度太宽(使用两个切口)
- 表面熔化
-
- 表面熔化
- 刀具不锋利
- 侧隙不足
- 冷却剂供给不足
- 粗加工面
- 进给太大
- 刀具刃磨不当
- 切削刃未磨锋利
- 螺旋纹
- 刀具退刀时有摩擦
- 刀尖毛刺
- 凹面或凸面
- 顶尖角太大
- 刀具与主轴不垂直
- 刀具偏向
- 进给太大
- 刀具安装在中心之上或之下
- 切削点有尖刺或毛刺
- 顶尖角不够大
- 刀具不锋利
- 进给太大
- 外径毛刺
- 切削直径前无倒角
- 刀具不锋利
- 表面熔化
下载完整的机械师工具箱
-
常用塑料加工工艺
-
此部分涵盖了最常用的塑料工程部件加工方法,为每一种部件都提供了获得最佳加工结果的指南和技巧。
正确加工对于到达零件尺寸要求和实现零件性能至关重要。加工不当会使完工零件产生应力,对其机械性能造成负面影响,且零件有提前失效的风险。
常见机械加工残余应力成因包括:
• 使用钝化或选型不当的刀具
• 转速和进给速率不当所产生的过多热量
• 通过加工去掉大量材料,通常是从型材一侧 -
何为车螺纹?何为攻丝?
车螺纹和攻丝是用于生产螺纹的两种加工方法。车螺纹是用板牙切出外螺纹的过程,而攻丝则是用丝攻在已钻好的孔内加工出螺纹的过程。
对塑料与金属进行车螺纹和攻丝对比
对塑料材料车螺纹和攻丝时的一个主要考量因素为,塑料比金属对缺口更敏感。在车螺纹过程中,尤其是在细牙加工程序中,一些聚合物材料可能会开裂
塑料的车螺纹加工技巧
需用硬质合金刀片在单个点上进行塑料车螺纹加工,结束时进行四到五次加工精度为 0.001" 走刀。建议使用冷却剂。
塑料的攻丝加工技巧
对塑料进行攻丝加工时,需使用特定的双槽丝攻。保持丝攻内无碎屑聚集。在攻丝过程中同样建议使用冷却剂。
-
何为铣削?
铣削是一种在静止塑料型材上使用高速圆柱形切割刀具进行加工的方法,铣削时,沿轴移动刀具以便从不同方向削除型材上的材料。计算机数字控制 (CNC) 铣削能改善塑料铣削的精度和效率。
塑料与金属的铣削对比
在铣削塑料时,至关重要的一点是将零件正确固定在工作台上,并将来自高速刀具的振动降至最低,否则可能会使型材移位,进而导致颤纹并降低精度。
塑料的铣削技巧
- 建议使用顺铣,又名同向铣削,而非传统铣削。
- 在铣床床身上进行充分固定,能实现工作台快速移动和主轴高速旋转。
- 当然,也不应将型材固定得太紧,因其可能会变形或回弹。
- 端面铣削时,请使用正几何形状刀体。
-
何为锯切?
锯切是一种用带锯、台锯或其他专用设备将材料切割成多个小块的加工方法。
塑料与金属的锯切对比
塑料与金属锯切之间的主要不同点在于,锯片所产生的热量会对塑料零件造成负面影响,因其软化和熔化温度更低。至关重要的一点是,在锯切塑料时考虑锯片速度、材料热属性以及型材厚度。
锯切刀具选择技巧
- 带锯应用场景广泛,用于直线、连续曲线以及不规则切割时效果很好。
- 对于直线切割,台锯很方便,且其具备足够马力,能用于切割多种厚度和较厚横截面(最厚可达 4")。
锯片选择技巧
- 具备 0° 锯齿前倾角以及 3° 至 10° 锯齿组的直锯和组合锯是普通锯切的上佳之选,这可以减少摩擦生热。
- 无胶凹磨圆锯片会产生厚达 3/4" 的光滑切口。
- 钨钢刀片耐磨且能实现优质表面光洁度。
-
何为钻孔?何为镗孔?
钻孔是一种利用尖头螺旋刀具生成圆柱形孔和通孔的加工方法。镗孔是一种将已钻好的孔加大或精加工的精加工工艺。
塑料与金属的钻孔对比
在钻孔操作过程中需考量塑料隔热特性,当孔深大于两倍孔径时尤其如此。过多热量聚集可能会导致剥落、表面粗糙和误差过大。
塑料钻孔技巧对于小孔径(1/32" 至 1")
- 高速钢制麻花钻头通常就已足够。
- 建议频繁退出(啄式钻孔)以促进排屑。
- 平螺旋(低螺旋线)钻头能更好地排屑。
对于大孔径(大于等于25.400 mm)
- 建议使用平螺旋(低螺旋线)钻头或打磨至顶角118°且钻刃余隙为9°至15°的通用型钻头。应打磨(锐化)钻刃前刀面并磨薄钻心。
- 避免手动进给,因为钻头夹紧机构可能会导致微裂纹。
- 通常,最好先用600至1000 rpm以及每转0.127 mm至0.381 mm的正进给钻一个导向孔(直径最大12.700 mm)。
- 需要用400至500 rpm以及每转0.203 mm至0.508 mm的进给来二次钻孔以扩大孔径。
对于缺口敏感性极强的材料(如 Ertalyte® PET-P和玻璃纤维增强材料)
- 包含钻孔和镗孔的两步骤工艺能将热聚集最小化并减小裂纹风险。
- 首先,用刀片钻头以500至800 rpm以及每转0.127 mm至0.381 mm的进给速率钻一个直径为25.400 mm的孔。
- 接着,用配有半径为0.381 mm至0.762 mm硬质合金刀片的镗杆以500至1000 rpm以及每转0.127 mm至0.254 mm的进给速率来将孔镗至最终尺寸。
-
何为车削?
车削是一种塑料型材围绕静止车床旋转的加工工艺。对于沿共同旋转轴对称的加工零件,车削尤其有用。
塑料与金属的车削对比
与其他塑料加工工艺一样,车削也会产生热量。为了防止塑料件受损,材料热性能以及转速、刀具选择和冷却剂的使用都需仔细考量。
塑料车削技巧
- 车削操作需要具用正几何形状以及已打磨周边的刀片。
- 已打磨周边和已抛光顶面通常能减少刀片上的材料聚集,实现更优的表面光洁度。
- 通常建议将细晶粒 C-2 硬质合金刀具用于塑料车削操作。
-
-
额外加工处理
-
取决于零件和加工工艺要求,可建议使用冷却剂和/或退火以改善成品效果。本节介绍适用于加工塑料零件的冷却剂和退火工艺。
-
何为冷却剂?
冷却剂能减少局部摩擦热量聚集,从而改善加工结果并延长刀具寿命。在加工工程塑料时常用的冷却剂有很多种,包括空气、干冰、喷雾以及专门开发的冷却剂。
何时建议使用冷却剂?大多数加工操作以及大多数工程塑料并不需要冷却剂。尽管如此,以下情况下仍建议使用冷却剂:
- 在对塑料进行钻孔或切割时,因为这两种工艺会产生大量摩擦热。
- 在加工缺口敏感性极强的材料时,如 Ertalyte® PET-P、Duratron® PAI、Duratron® PBI 和玻璃纤维或碳纤维增强产品。
- 为实现优质表面光洁度和窄误差而有必要时。
冷却剂选择技巧
- 喷雾和压缩气体是冷却切割界面非常有效的方法。
- 虽然通用型石油基切削液适用于许多金属和塑料,但可能导致无定形塑料应力开裂,如 Altron™ PC、Sultron® PSU、Sultron® PPSU 和 Duratron® U1000 PEI。
- 适用于大多数塑料的两种射流冷却剂为 Trim E190 和 Tim Sol LC SF。
-
何为退火?
退火是一种热处理工艺,能改善塑料的物理性能,增加其延展性并减少其硬度,使型材更易于加工。退火有助于释放塑料内应力,赋予已加工零件更高的长期尺寸稳定性。退火工艺要求将塑料型材加热至其熔化温度的二分之一并保持既定时长,然后让其以特定速度冷却。
加工前退火
来自 Mitsubishi Chemical Group“先进材料”部门的所有塑料型材均已用专利去应力循环来退火,该循环能将所有可能由制造工艺所导致的内部应力最小化。这能确保材料尺寸在加工过程中以及加工后保持稳定。
加工后退火
鲜有已加工塑料零件需要在加工后进行退火以满足尺寸或性能要求;尽管如此,加工后退火确实有若干益处,包括:
- 提升耐化学性 – PC、PSU 和 PEI 材料能从加工后退火中获益,减少应力龟裂。
- 获得更佳平直度和更窄误差 – 要求精确平直度和非对称轮廓的极窄误差零件有时需要在加工操作之间进行工序间退火。
- 高压力速度和低磨损 PAI -要求高压力速度或尽可能低磨损系数的挤出或注塑成形 Duratron® PAI 零件能从加工后的额外固化中获益。此固化工艺能优化耐磨性能。只有 PAI 能从此循环中获益。
塑料退火技巧- 通过粗加工、退火和用非常小的切削量来精加工,可实现更好的平直度。
- 为减少潜在的加工所致应力,请查看特定材料的制造指南。请注意,指南会随材料类型的变化而变化。
- 确保已用夹具将零件固定至所需形状或平直度以防止变形。在零件已完成整个循环且触摸时感觉不热之后,才能松开零件。
- 退火之后应进行精加工,以达到关键尺寸要求。
- 若横截面较薄,则可更改加热和保温时间。
-
-
工程塑料排障指南
-
- 锥形孔
- 钻头刃磨不当
- 间隙不足
- 进给太大
- 表面烧蚀或熔化
- 钻头类型错误
- 钻头刃磨不当
- 进给太小
- 钻头不锋利
- 钻心太厚
- 表面剥落
- 进给太大
- 间隙太大
- 前刀面太大(表述为钻心偏薄)
- 振刀
- 间隙太大
- 进给太小
- 钻头伸出过长
- 前刀面太大(表述为钻心偏薄)
- 内径有进给痕或螺旋线
- 进给太大
- 钻头未对中
- 钻头打磨未对中
- 孔径过大
- 钻头打磨未对中
- 钻心太厚
- 间隙不足
- 进给速率太快
- 顶尖角太大
- 孔径过小
- 钻头不锋利
- 间隙太大
- 顶尖角太小
- 孔不同心
- 进给太大
- 主轴转速太慢
- 钻头钻入下一工件太深
- 切削刀具留下的尖刺使钻头偏向
- 钻心太厚
- 钻头起始转速太快
- 钻头未装在中心位置
- 钻头刃磨不当
- 切削毛刺
- 切削刀具不锋利
- 钻头未完全穿过工件
- 钻头迅速变钝
- 进给太小
- 主轴转速太快
- 冷却剂润滑不足
- 锥形孔
-
- 表面熔化
- 太钝或后棱摩擦
- 侧隙不足
- 进给速率太慢
- 主轴转速太快
- 粗加工面
- 进给太大
- 间隙角错误
- 刀具刀尖过于尖锐(要求刀尖稍微倒圆)
- 刀具未装在中心位置
- 切削边缘毛刺
- 尖锐角未倒角
- 刀具不锋利
- 侧隙不足
- 刀具上无导程角(刀具应逐步而非突然从切削处退出)
- 角落处裂纹或剥落
- 刀具正前刀面太大
- 刀尖并非慢慢切入
- 刀具不锋利
- 刀具安装在中心之下
- 刀具刀尖过于尖锐(要求刀尖稍微倒圆)
- 振刀
- 刀尖倒圆半径太大
- 刀具未安装牢固
- 材料支撑不当
- 切削宽度太宽(使用两个切口)
- 表面熔化
-
- 表面熔化
- 刀具不锋利
- 侧隙不足
- 冷却剂供给不足
- 粗加工面
- 进给太大
- 刀具刃磨不当
- 切削刃未磨锋利
- 螺旋纹
- 刀具退刀时有摩擦
- 刀尖毛刺
- 凹面或凸面
- 顶尖角太大
- 刀具与主轴不垂直
- 刀具偏向
- 进给太大
- 刀具安装在中心之上或之下
- 切削点有尖刺或毛刺
- 顶尖角不够大
- 刀具不锋利
- 进给太大
- 外径毛刺
- 切削直径前无倒角
- 刀具不锋利
- 表面熔化
-
-
下载完整的机械师工具箱
-
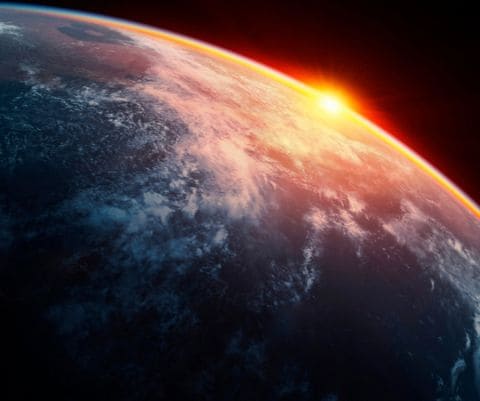