Plastic material selection guide
Better design, improved performance, faster manufacturing, and reduced production time and cost are a just a few of the reasons why OEMs are making the switch to engineering plastics. This 5-step guide will help you choose the optimal thermoplastic material that will perform in every way you need.
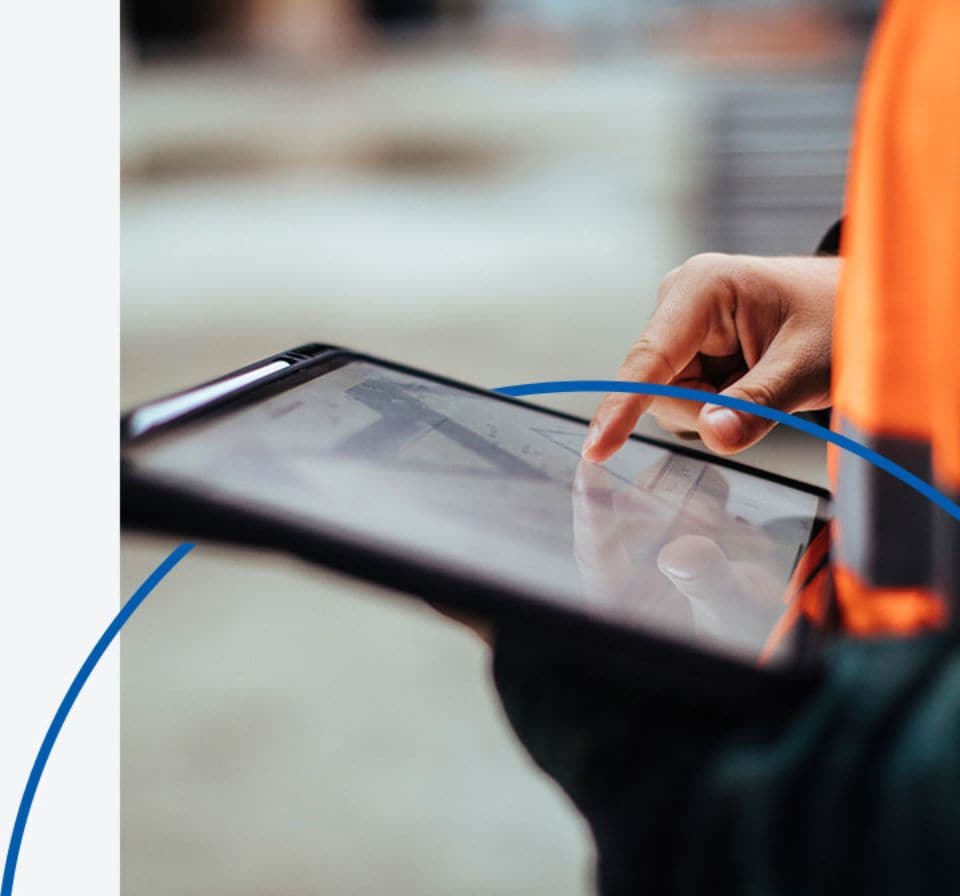
High-performance plastics are increasingly being used to replace materials like bronze, stainless steel, aluminium, and ceramics. The most popular reasons for switching to plastic include:
- Longer part life
- Elimination of lubrication
- Reduced wear on mating parts
- Faster operation of equipment/line speeds
- Less power needed to run equipment
- Corrosion resistance and inertness
- Weight reduction
With the many plastic materials available today, selecting the right one for your application may be intimidating. To help, we’ve created the following guidelines to assist those new to the world of engineering plastics.
1. What is the general application purpose?
-
Is it a bearing and/or wear application?
Wear properties are enhanced by MoS2, graphite, carbon fiber, and polymeric lubricants (PTFE, waxes). For bearing and wear applications, the first consideration is wear performance expressed in PV and k-factor. Calculate the PV (pressure (psi) x velocity (m/min)) required. Using the scatter chart below as reference, select materials whose limiting PV's are above the PV you have calculated for the application. Further selection can be made by noting the k-factor of your material choices. In general, the lower the k-factor, the longer the wear life of the material.
Is it a static or dynamic structural application?
Structural components are commonly designed for maximum continuous operating stresses equal to 25% of their ultimate strength at a specific temperature. This guideline is meant to compensate for the viscoelastic behavior of plastics that result in creep. Isometric stress-time curves are provided below to help you characterize a material's strength behavior as a function of time at both room temperature and at 150 °C (300 °F).
2. What are the thermal requirements of the plastic material?
-
HDT is an indication of a material's softening temperature and is generally accepted as a maximum temperature limit for moderately to highly stressed, unconstrained components.
-
Continuous service temperature is generally reported as the temperature above which significant, permanent physical property degradation occurs after long term exposure. This guideline is not to be confused with continuous operation or use temperatures reported by regulatory agencies such as Underwriters Laboratories (UL).
-
The melting point of crystalline materials and glass transition temperature of amorphous materials are the short-term temperature extremes to which form stability is maintained. For most engineering plastic materials, using them at or above these temperatures should be avoided.
3. Which chemicals will the plastic material be exposed to?
-
The requirements for chemical resistance in any given application can be difficult to predict since concentration, temperature, time, and stress each have a role in defining suitability for use. For this reason, we strongly recommend that you test materials under end-use conditions.
Generally speaking, thermoplastics have the advantage of exhibiting a broad range of chemical resistance behavior, making it possible to select a plastic material that can perform to the specifications of your application.
For instance, nylons, acetals, and Ertalyte™ PET-P have chemical resistance properties that make them generally suitable for interaction with the chemicals in most standard industrial environments. Beyond standard applications, high-performance, crystalline materials such as Fluorosint™ filled PTFE, Techtron™ PPS and Ketron™ PEEK are more suitable for aggressive chemical environments.
4. Consider additional criteria
-
- Relative impact resistance/toughness
- Dimensional stability
- Flammability
- Electrical properties
- UV resistance, radiation resistance, autoclavability, outgassing,etc.
- Regulatory/agency compliance
Materials with higher tensile elongation, Izod impact, and tensile strengths are generally tougher and less notch sensitive for shock loading applications.
-
Engineering plastics can expand and contract with temperature changes at rates of 2 to 20 times more than many metals. The coefficient of linear thermal expansion (CLTE) is used to estimate the expansion rate for engineering plastic materials. CLTE is reported both as a function of temperature and as an average value. Figure 6 shows how many different engineering plastics react to increased temperature.
Modulus of elasticity and water absorption also contribute to the dimensional stability of a material. Be sure to consider the effects of humidity and steam.
-
Agencies such as the Food and Drug Administration (FDA), U.S. Department of Agriculture (USDA), Underwriters Laboratory (UL), 3A-DairyAssociation,and American Bureau of Shipping (ABS) commonly approve or set specific guidelines for material usage within their industrial segments.Use these frameworks as a starting point for reviewing material performance data.
5. Which plastic shape is best for your part?
-
Mitsubishi Chemical Group offers designers the broadest availability of sizes and configurations for thermoplastic shapes and semi-finished parts. By investigating all the shape possibilities, you can reduce your fabrication costs by obtaining the most economical shape.
Here is a brief overview of the processing methods we recommend for different sorts of shapes:
Shape description Best processing method Long lengths
Small diametersExtrusion Rod, plate, strip, profiles, tubular bar, bushing stock Large stock shapes
Near net shapesCasting Rod, plate, tubular bar, near net configurations Small shapes in advanced engineering materials Compression molding Rod, disc, plate, tubular bar Small shapes in advanced engineering materials
Small diametersInjection molding Rod, disc, plate, tubular bar Note: From process to process, many material choices remain the same. However, there are physical property differences based upon the processing technique used to make the shape.
For example:
- Injection molded parts exhibit the greatest anisotropy (properties are directionally dependent).
- Extruded products exhibit slightly anisotropic behavior.
- Compression moldedproducts are isotropic —they exhibit equal properties in all directions.
-
The machinability of a thermoplastic should also factor into your material selection process. Materials that are more difficult and therefore costly to machine may be unsuitable for parts that are especially intricate.
All thermoplastic materials from Mitsubishi Chemical Groupare stress relieved to enhance machinability. In general, glass- and carbon-reinforced grades are considerably more abrasive on tooling and are more notch sensitive during machining than are unfilled grades. On the other hand, reinforced grades are commonly more stable during machining.
Because of their extreme hardness, imidized materials (i.e. Duratron™ PAI, Duratron™ PI, and Duratron™ PBI) can be challenging to fabricate. Carbide and polycrystalline diamond tools should be used during machining of these materials. To assist you in assessing machinability, review the relative machinability rating of our products.
-
1. What is the general application purpose?
-
Is it a bearing and/or wear application?
Wear properties are enhanced by MoS2, graphite, carbon fiber, and polymeric lubricants (PTFE, waxes). For bearing and wear applications, the first consideration is wear performance expressed in PV and k-factor. Calculate the PV (pressure (psi) x velocity (m/min)) required. Using the scatter chart below as reference, select materials whose limiting PV's are above the PV you have calculated for the application. Further selection can be made by noting the k-factor of your material choices. In general, the lower the k-factor, the longer the wear life of the material.
Is it a static or dynamic structural application?
Structural components are commonly designed for maximum continuous operating stresses equal to 25% of their ultimate strength at a specific temperature. This guideline is meant to compensate for the viscoelastic behavior of plastics that result in creep. Isometric stress-time curves are provided below to help you characterize a material's strength behavior as a function of time at both room temperature and at 150 °C (300 °F).
-
-
2. What are the thermal requirements of the plastic material?
-
HDT is an indication of a material's softening temperature and is generally accepted as a maximum temperature limit for moderately to highly stressed, unconstrained components.
-
Continuous service temperature is generally reported as the temperature above which significant, permanent physical property degradation occurs after long term exposure. This guideline is not to be confused with continuous operation or use temperatures reported by regulatory agencies such as Underwriters Laboratories (UL).
-
The melting point of crystalline materials and glass transition temperature of amorphous materials are the short-term temperature extremes to which form stability is maintained. For most engineering plastic materials, using them at or above these temperatures should be avoided.
-
-
3. Which chemicals will the plastic material be exposed to?
-
The requirements for chemical resistance in any given application can be difficult to predict since concentration, temperature, time, and stress each have a role in defining suitability for use. For this reason, we strongly recommend that you test materials under end-use conditions.
Generally speaking, thermoplastics have the advantage of exhibiting a broad range of chemical resistance behavior, making it possible to select a plastic material that can perform to the specifications of your application.
For instance, nylons, acetals, and Ertalyte™ PET-P have chemical resistance properties that make them generally suitable for interaction with the chemicals in most standard industrial environments. Beyond standard applications, high-performance, crystalline materials such as Fluorosint™ filled PTFE, Techtron™ PPS and Ketron™ PEEK are more suitable for aggressive chemical environments.
-
-
4. Consider additional criteria
-
- Relative impact resistance/toughness
- Dimensional stability
- Flammability
- Electrical properties
- UV resistance, radiation resistance, autoclavability, outgassing,etc.
- Regulatory/agency compliance
Materials with higher tensile elongation, Izod impact, and tensile strengths are generally tougher and less notch sensitive for shock loading applications.
-
Engineering plastics can expand and contract with temperature changes at rates of 2 to 20 times more than many metals. The coefficient of linear thermal expansion (CLTE) is used to estimate the expansion rate for engineering plastic materials. CLTE is reported both as a function of temperature and as an average value. Figure 6 shows how many different engineering plastics react to increased temperature.
Modulus of elasticity and water absorption also contribute to the dimensional stability of a material. Be sure to consider the effects of humidity and steam.
-
Agencies such as the Food and Drug Administration (FDA), U.S. Department of Agriculture (USDA), Underwriters Laboratory (UL), 3A-DairyAssociation,and American Bureau of Shipping (ABS) commonly approve or set specific guidelines for material usage within their industrial segments.Use these frameworks as a starting point for reviewing material performance data.
-
-
5. Which plastic shape is best for your part?
-
Mitsubishi Chemical Group offers designers the broadest availability of sizes and configurations for thermoplastic shapes and semi-finished parts. By investigating all the shape possibilities, you can reduce your fabrication costs by obtaining the most economical shape.
Here is a brief overview of the processing methods we recommend for different sorts of shapes:
Shape description Best processing method Long lengths
Small diametersExtrusion Rod, plate, strip, profiles, tubular bar, bushing stock Large stock shapes
Near net shapesCasting Rod, plate, tubular bar, near net configurations Small shapes in advanced engineering materials Compression molding Rod, disc, plate, tubular bar Small shapes in advanced engineering materials
Small diametersInjection molding Rod, disc, plate, tubular bar Note: From process to process, many material choices remain the same. However, there are physical property differences based upon the processing technique used to make the shape.
For example:
- Injection molded parts exhibit the greatest anisotropy (properties are directionally dependent).
- Extruded products exhibit slightly anisotropic behavior.
- Compression moldedproducts are isotropic —they exhibit equal properties in all directions.
-
The machinability of a thermoplastic should also factor into your material selection process. Materials that are more difficult and therefore costly to machine may be unsuitable for parts that are especially intricate.
All thermoplastic materials from Mitsubishi Chemical Groupare stress relieved to enhance machinability. In general, glass- and carbon-reinforced grades are considerably more abrasive on tooling and are more notch sensitive during machining than are unfilled grades. On the other hand, reinforced grades are commonly more stable during machining.
Because of their extreme hardness, imidized materials (i.e. Duratron™ PAI, Duratron™ PI, and Duratron™ PBI) can be challenging to fabricate. Carbide and polycrystalline diamond tools should be used during machining of these materials. To assist you in assessing machinability, review the relative machinability rating of our products.
-
Looking to talk to a material selection expert? Get in touch with our specialist teams by filling in the contact form. We’re ready to meet your next challenge.
Contact us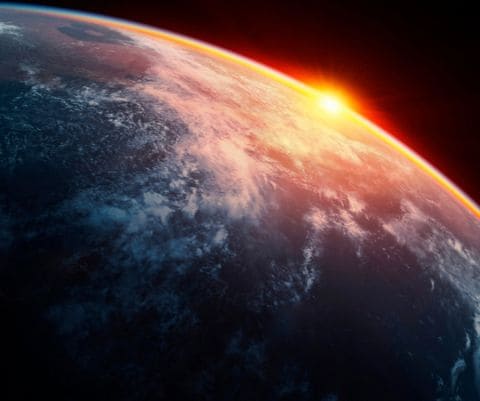