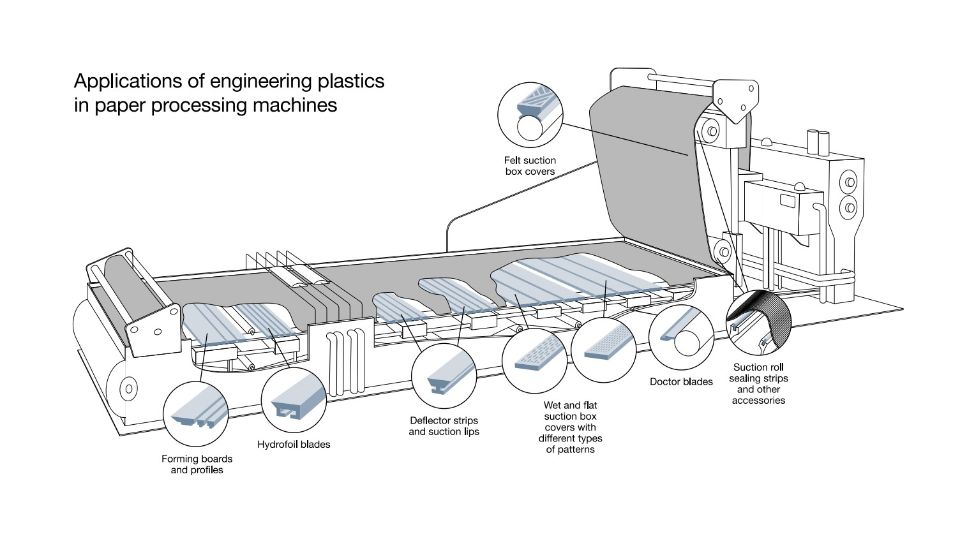
Advanced materials that prevent build-up of fibers and particles in paper and pulp processing.
Are your ceramic or polyurethane parts failing prematurely due to the high-temperature and wear conditions present in dewatering systems? High-performance TIVAR™ UHMW-PE and Ketron™ PEEK materials from Mitsubishi Chemical Group exhibit the heat resistance and sliding properties needed to provide lasting performance in the paper and pulp milling industries.
For decades, these specially developed material grades have been successfully used by manufacturers of paper-making and dewatering machines in more than 40 countries.
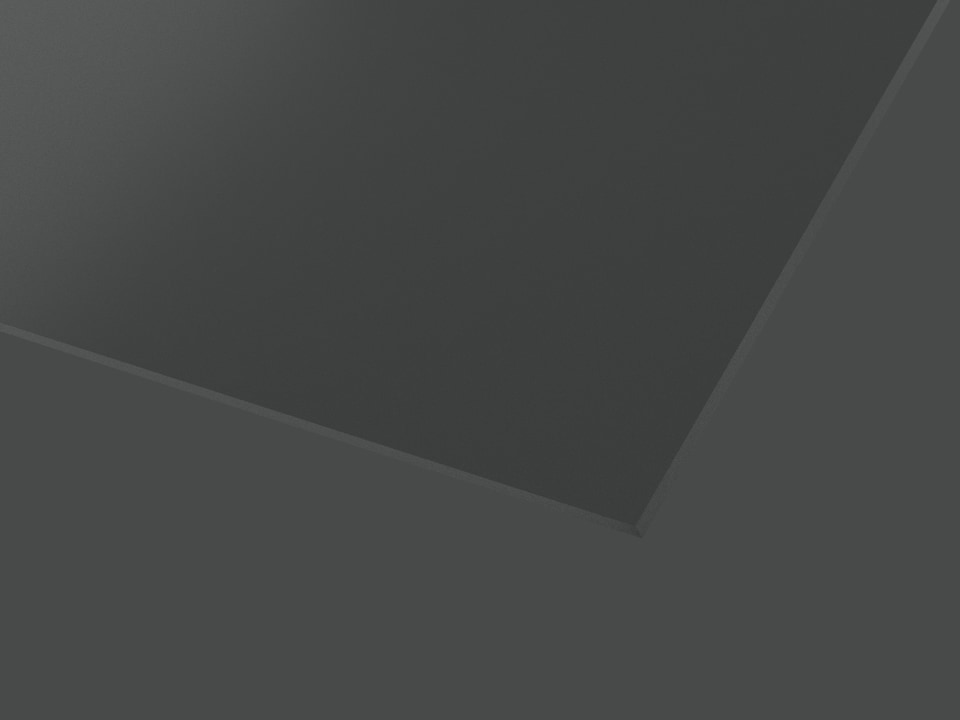
The challenge: In a paper mill, suction box covers act as a barrier between the paper and a vacuum source used to pull moisture from the paper. In high-temperature zones near heaters or ovens, suction box covers could be subject to temperatures ranging from 360°F - 405°F (182°C - 207°C), precluding the use of standard polyurethane or polyethylene. However, while ceramic could hold up to the high temperatures, the material experienced wear problems that resulted in a shorter-than-desired lifecycle for the customer.
The solution: Ketron™ HPV PEEK was selected to create the new suction box covers for its consistent performance in temperatures as high as 482°F (250°C), excellent wear resistance, and dimensional stability.
The results: The new PEEK suction box covers exhibited the ideal mechanical strength and temperature resistance for the application, as well as the dimensional stability required to maintain tolerance control of the machined-in slots. With dramatically improved wear performance, the Ketron™ HPV PEEK covers exhibited a 30% longer service life over the ceramic parts, helping to improve production efficiency.
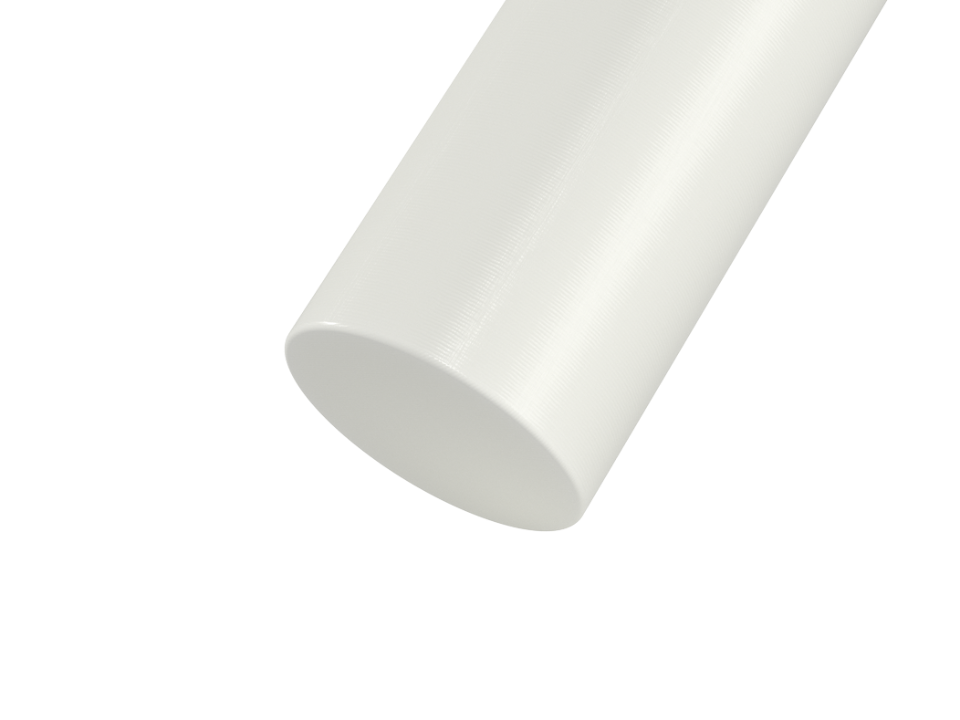
The challenge: An OEM of dewatering machines for the pulp industry was using a polyurethane material to produce spray nozzles in-house. These nozzles are especially used for dewatering screens in production processes for hardwoods. However, the PU plastic was only somewhat effective as the continuous temperatures of 200°F (93°C) were causing the nozzles to deteriorate quickly.
The solution: TIVAR™ H.O.T. UHMW-PE was selected as a replacement for the polyurethane for its excellent resistance to hot water, continuous service temperature of 275°F (110°C), and stock shape availability as a rod for easy machining.
The results: The OEM has been successfully using TIVAR™ H.O.T. UHMW-PE rods to fabricate pulp nozzles for over 15 years. The components made from TIVAR™ H.O.T. outlast the old polyurethane nozzles by as much as five to six times.
Looking for something specific? Get in touch with our specialist teams by filling in the contact form. We’re ready to meet your next challenge.
Contact us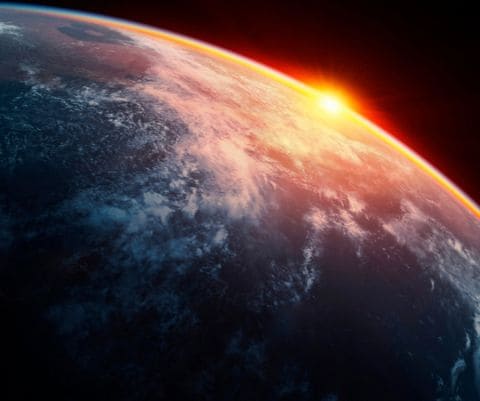