Wear resistance is the ability of a material to resist the progressive loss of volume from its surface through mechanical actions such as repeated rubbing, sliding, or scraping.
Wear-resistant materials minimize friction between mating surfaces, allowing parts to retain their form and integrity for longer in applications involving contact between load-bearing surfaces.
Our portfolio contains a wide variety of engineering plastics that minimize wear through either low-friction properties or self-lubrication, reducing mechanical wear while upholding performance standards in application.
The principles of wear, friction, and lubrication are studied in the field of tribology – the science and engineering of the interaction between surfaces in relative motion.
Wear-resistant parts and components are critical in engineering applications where two load-bearing surfaces slide over one another, such as in bearings, wear pads, gears, and rotating shafts.
Wear-resistance is also critical wherever mated surfaces must retain their form to ensure function e.g. in conformal contact applications where components are precisely machined to maximize efficiency.
Many engineering applications demand low-friction, wear-resistant materials, such as thermoplastics. Engineering plastics generally have a lower coefficient of friction than metals in the same or similar applications. Additionally, high-performance plastic materials often have self-lubricating properties, making them ideal for extended wear and use in load-bearing applications.
Semi-crystalline thermoplastics in particular perform extremely well in wear, bearing, and friction applications due to their toughness and sharp melting points. Acetal (POM), nylon (PA), ultra-high molecular weight polyethylene (UHMW-PE), polyphenylene sulfide (PPS), polyether ether ketone (PEEK), and polyamide-imide (PAI) are among the most common wear-resistant thermoplastic materials used for parts and components in high-friction contact with metals.
Compared with metals or other mating surfaces, wear-resistant engineering plastics offer several advantages in high-friction applications:
-
Low friction and self-lubricating properties reduce the need for lubrication
-
Predictable wear rate reduces unplanned maintenance and downtime
-
Improved operating reliability and extended mean time between repair (MTBR)
-
Reduced noise between mated parts
-
In food contact applications, reduced risk of contamination from material swarf and lubricant
Conveyor bearings from Techtron™ HPV PPS
The challenge: In a facility that melts plastic waste and extrudes it into recycled rods, metallic bearings on the material conveyors required excessive maintenance. The warm production environment generated steam, thinning the grease on the metal bearings, leading to increased wear and causing the conveyors to seize.
The solution: Our Techtron™ HPV PPS material was used to produce low-friction, self-lubricating insert bearings that could be snapped into the existing metallic pillow and flange blocks on the conveyors.
The results: In addition to eliminating the need for lubrication, our high-performance PPS bearings retained wear and strength properties at warm temperatures, resisted corrosion, and displayed dimensional stability both on machining and in the steamy production environment.
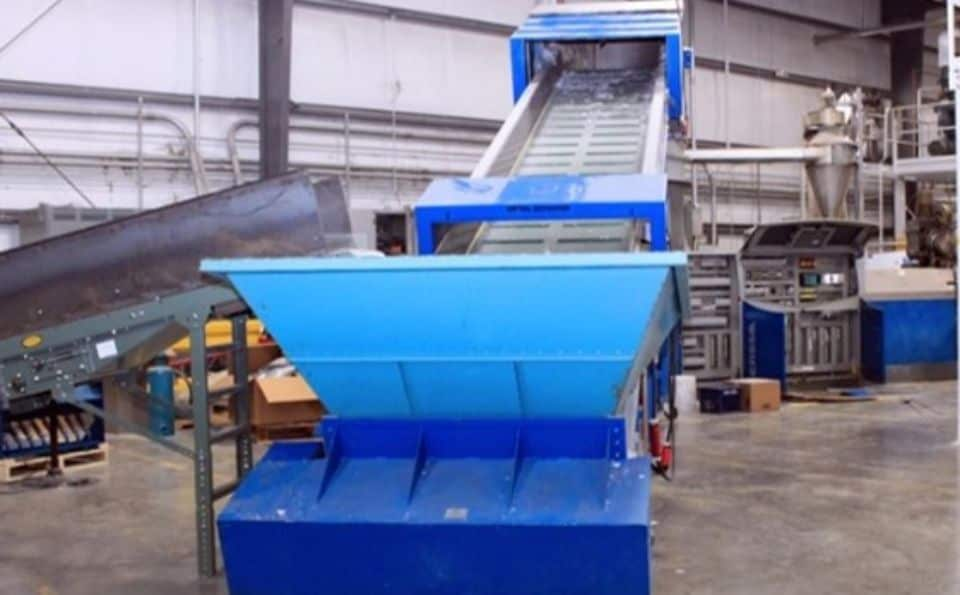
Pivot bushings for solar panels from TIVAR™ UV UHMW-PE
The challenge: To absorb as much solar energy as possible, photovoltaic panels can pivot to follow the path of the sun. Enabling this motion required a conformal pivot bushing that would retain its form and performance properties throughout the day, and also for outdoor use and UV-exposure.
The solution: Our TIVAR™ UV UHMW-PE material was selected for its long-wearing properties and excellent stability in outdoor environments.
The results: Low-friction, low-noise, UV-resistant, and self-lubricating, the TIVAR™ UV bushings not only display the ideal wear properties for the application, they also retain these properties throughout the warranty period. They absorb no moisture, and the lubrication does not corrode or freeze, eliminating the need for maintenance despite constant exposure to the elements.
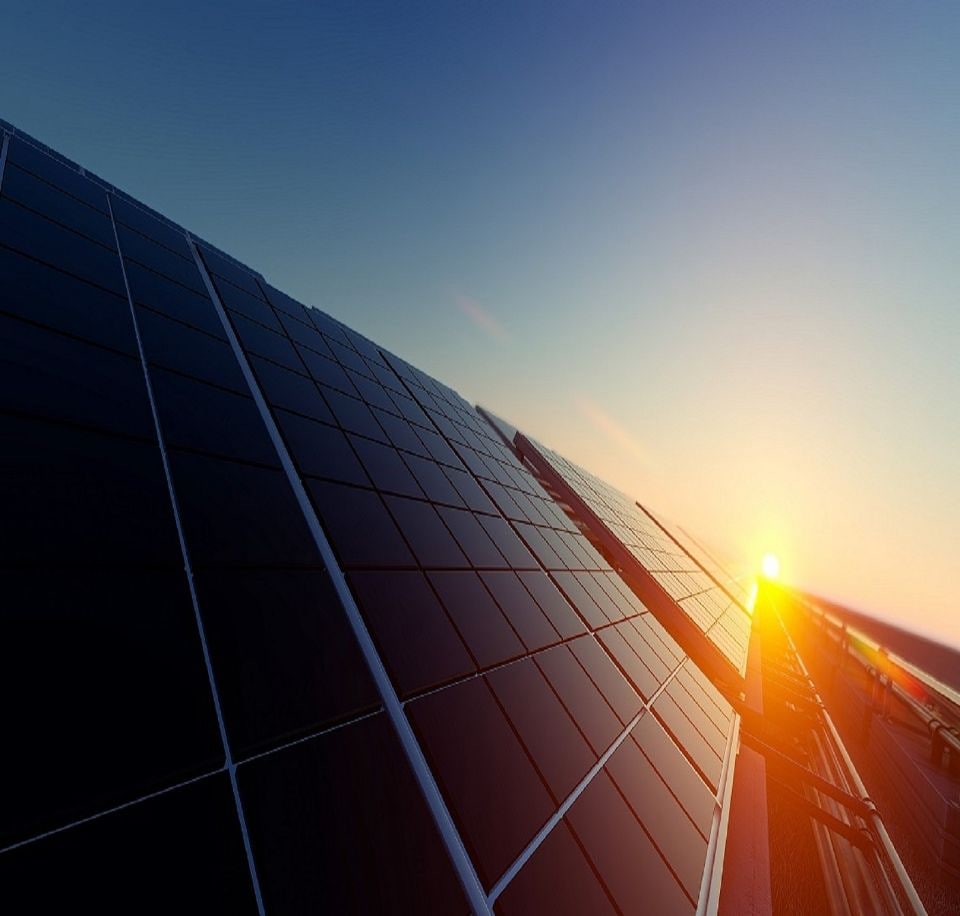
Reducing costs and aerospace emissions with self-lubricating wear strips for wing flaps
Our self-lubricating Duratron™ T4301 PAI material was used to create a component that replaces the need for complex, labor-intensive parts.
Our wear-resistant PAI solution resulted in a lighter plane with a lower risk of failure, reducing both maintenance and emissions. Our part was so effective, it has since been adopted across the Aerospace industry.
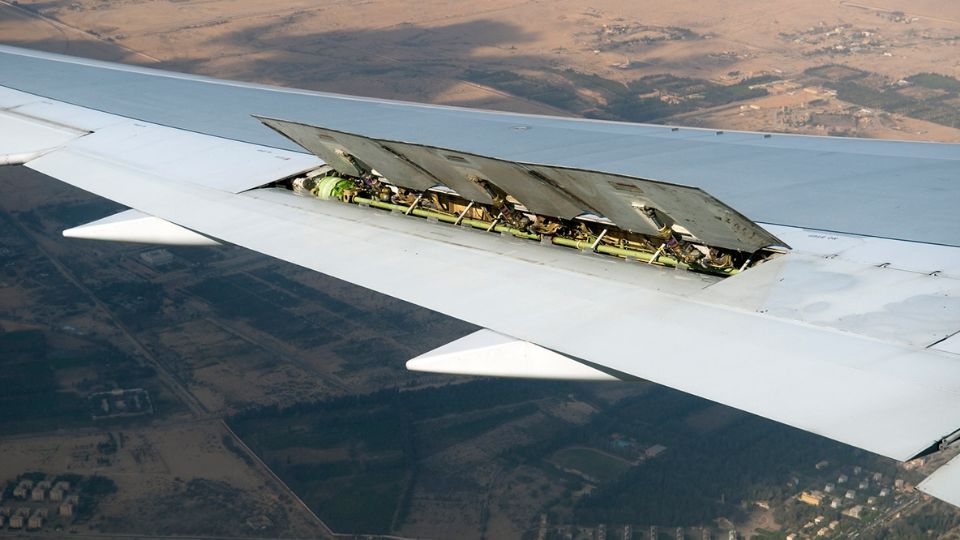
-
The coefficient of friction (CoF) is a measurement of the resistance generated when sliding the surface of one material over another. The standard method of deriving CoF values for thermoplastic materials is the ASTM D3702, which makes it possible to compare materials and predict their wear performance.
In ASTM D3702 testing, a polymeric sample is placed upon a polished steel thrust washer. A normal force is applied, followed by torque to get the plastic rotating. The CoF value is derived from the ratio of the two forces acting upon the mating surfaces: the sliding force (torque) and the normal force. The lower this ratio, the slicker the material.
There are two different CoF values that are important for understanding our materials’ frictional behavior: the static CoF and the dynamic CoF.
The static CoF refers to the ratio of the sliding force to the normal force at initial movement, going from rest to rotation. The dynamic CoF refers to the ratio of these forces once the washer is already in motion. Typically, the static CoF is higher than the dynamic CoF, as greater force is needed to initiate motion than to maintain it. Stick-slip occurs when the static and dynamic CoF values are too far apart, resulting in an unwanted jerking motion as the mating surfaces transition.
-
The wear rate, also known as the K factor, is a measure of a material’s resistance to wear. To calculate the K factor of an engineering plastic, we apply the QTM 55010 test method, which uses a journal bearing rather than a thrust washer.
The K factor is calculated from the variables of pressure (the applied load), velocity, and elapsed time. The lower the K factor, the greater the wear resistance of the tested material.
-
The limiting pressure velocity, or limiting PV, is a metric expressing the maximum compression that a mated surface can bear.
The limiting PV helps engineers understand which pressure and velocity conditions can generate excessive frictional heat, causing the system to fail.We calculate the limiting PV with the QTM 55007 method on the basis of the applied load over a given surface area and the velocity of the torque. The higher the limiting PV, the more compression and frictional heat the material can withstand.
Get in touch with our specialist teams by filling in the contact form. We’re ready to meet your next challenge.
Contact us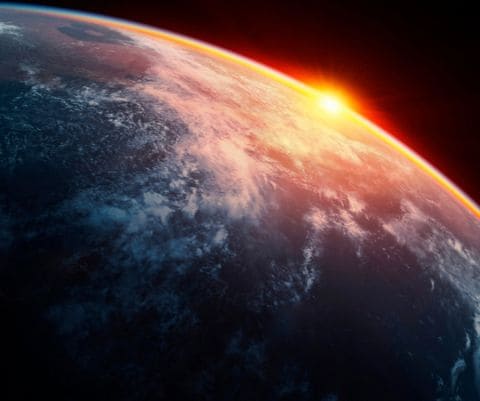